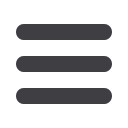

Technology News
Tailor drawn technique
AGAINST the background of increasing
requirements for lower weights in the
automotive industry, the tailor drawn
tubes (TDT) technique has become
more important. Existing methods for
the production of these special tubes
can only be applied experimentally and
are, therefore, labour intensive.
According to Bültmann GmbH,
Germany, the increased demands for
narrow tolerances can only be fulfilled
by current technical possibilities with
difficulty. Furthermore it is not possible
to achieve a ‘steady’ process reliability
based on current technology. Due to
the numerous influencing parameters
in the TDT drawing technology, the
tube drawing process currently used
will soon reach its technical limits.
Intensive development work and
positive practical experience enables
Bültmann to assist customers in
combining theory and practice.
Bültmann’s patented TDT Production
System, in conjunction with the
company’s draw bench technology,
can now be implemented in the tube
production industry.
When developing the TDT tube
drawing technology, Bültmann attached
greatest importance to the possibility
of using technological components
that have already been used for other
applications.
In order to achieve very narrow
tolerances, especially in the transition
zone of wall thickness, and to ensure
the necessary process reliability at the
same time, a closed control circuit is
indispensable.
This process control is assured
by combining sensible and very
dynamically reacting drive systems and
specially designed measuring devices
and process software.
You can visit Bültmann GmbH at
Stand 6E39 at Tube Düsseldorf 2016.
Bültmann GmbH
– Germany
Fax: +49 2394 18171
Email:
info@bueltmann.comWebsite:
www.bueltmann.comStraight
tubes
ABSOLUTE straightness is one of the
concise quality criteria in the production
of round bars and pipes. Bendcheck –
the precision laser measuring system
from Zumbach – monitors bending
continuously without missing any
sections directly within the production
process. This replaces the ODAC
®
laser measuring heads used currently
to manually spot test with a non-contact
online test for bending. Apart from the
obvious gain in quality, the manufacturer
also saves considerable time through
the use of the online date check.
Bendcheck can be used for
synchronous real time scanning in
the production process, and quality
assurance directly after the straightening
process, without time consuming and
laborious checks with manual tools.
Zumbach Electronic AG
– Switzerland
Website:
www.zumbach.com • With up to 8 cameras. Modular camera setting, any shape can be captured • Up to 16,000 points / contour (2,048/camera) = 5,734,400 points/second (with 8 cameras) • Different colors of the lasers, thus no interference • Shape fault detection (SFD) • Creation of measurement recipe with Zumbach software: – Customer can load the profile via its own DXF file (from CAD construction) or – By means of the "Product Generator": predefined forms allow quick "read in" of any product with round or rectangular size PROFILEMASTER® SPS Series. In-Line Light Section Profile Measurements Systems For Hot and Cold Applications Measure and Validate Your Profile Provides real-time dimensional, shape and angular measurement as well as cross-sectional display ZUMBACH Electronics sales@zumbach.ch I www.zumbach.com Learn more about PROFILEMASTER® 4 – 8 April 2016 Booth # 05 E17