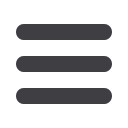

Inspection, testing & qual ity control
www.read-tpt.com66
J
anuary
2016
Tubular inspection services
TUBOSCOPE, a division of National
Oilwell Varco, is a supplier of tubular
inspection services and equipment to
the petroleum and pipe manufacturing
industry. Its technologies allow
inspection of new and used tubular
goods to demanding industry and
customer specifications.
The
company’s
systems
include Amalog
®
and Sonoscope
®
electromagnetic inspection technologies,
and Truscope
®
, TruWall
®
, and TruScan
®
ultrasonic (UT) inspection systems.
Tuboscope supplies mill inspection
equipment, available to manufacturers
of tubular goods worldwide, that can be
employed to effectively inspect tubulars
as rapidly as they are fabricated. These
mill units are capable of operating at
high testing speeds and can be custom-
designed to production line requirements.
An example of this capability within the
Tuboscope product line is the Truscope
A/S, which stands for Truscope-Amalog-
Sonoscope. This inspection system
combines the non-destructive techniques
of EMI (electro-magnetic induction) and
UT (ultrasonic) principles to detect,
evaluate and classify, in a single pass of
the pipe through the system, transverse
and longitudinal, internal and external
flaws as well as wall thickness variations
and laminations.
The Truscope A/S system provides
full-body inspection across a large range
of pipe diameters. These pipes can be
seamless or ERW, manufactured of
ferrous or non-ferrous alloy materials,
and with a variety of end conditions –
saw-cut or cropped; plain-end; threaded;
coupled; and upset or non-upset.
NOV Wellbore Technologies
– USA
Fax: +1 713 799 5452
Website:
www.nov.comEMI inspection for OCTG industry
MANY OCTG MFL (magnetic flux
leakage)
inspection
equipment
manufacturers claim their machines
detect flaws on 0.545" (13.84mm)
walls and greater during the inspection
process, but often these claims ignore a
key component of a quality inspection –
repeatability.
API 5CT specifications require a
minimum of 20 per cent repeatability on
all inspection runs. Often the detectability
specifications given by EMI vendors to
the steel mills, processors or inspection
companies are a reflection of the
equipment manufacturer’s upper limits
of detection capabilities, or best case
scenarios – and they hope to address
the repeatability of their equipment
much later in the vendor selection
process. “In our opinion, there needs
to be more focus on repeatability much
earlier in the technical evaluations,”
said Danny Uselton, president of Scan
Systems Corp.
In EMI inspection, repeatability comes
down to the equipment’s hardware
and software capabilities to identify
the signal given by an imperfection
or artificial reference indicator and
report those imperfections at a similar
amplitude, consistently and repeatedly.
The equipment must have the capability
to pick up the flaw and break the alarm
threshold each and every time in order
to provide the level of confidence in
the inspection that API requires. If the
signal from a flaw falls within an area
of significant noise generated from the
pipe, it may stand out during one pass
(detected), but get lost “in the grass”
during the next run (repeatability). Using
advanced signal processing algorithms
combined with proprietary sensors and
cutting-edge signal detection hardware,
Scan Systems’ Pitco M-Series with ESP
upgrade has dramatically improved the
ability to separate a flaw’s signal from the
background noise, and is claimed to offer
the best S:N ratio on any given pipe in
the industry.
Matt Rutledge, general manager/VP of
Scan Systems, believes that repeatability
is a top priority and something customers
should ask about sooner in the vendor
selection process. “Surprisingly, many
steel mills, processors and third party
inspection companies neglect to inquire
about the inspection equipment’s
capabilities in regards to repeatability
until much later in the selection process.”
While 0.4" (10mm) pipe wall thickness
has historically been the limit for
existing EMI/MFL inspection equipment,
Scan Systems’ Pitco M-Series with
ESP upgrade can reliably detect and
repeat on N5 ID notches up to 0.545"
(13.84mm) wall thickness and N10 ID
notches up to 0.625" (15.875mm) walls.
This ability to accurately detect and
repeat on these types of indications
has been accomplished through the
hard work and determination of the
employees in the R&D department of
Scan Systems Corporation.
Scan Systems Corp
– USA
Email:
mattr@scansystems.comWebsite:
www.scansystems.comThe Pitco M-Series from Scan Systems