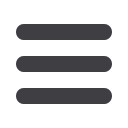

Technology News
www.read-tpt.com62
J
anuary
2016
Bending efficiency with low emissions
HIGH efficiency, low emissions and
cost-optimised construction processes
are the main demands for power plants
and their construction. Pipelines have
an essential significance. On the one
hand tubes or pipes made of wear-
resistant and resilient material, as well
as small bending radii, enhance the
degree of efficiency of power plants.
On the other hand, lean tube bending
processes and automated production
lines provide a decisive contribution
to cost efficiency in power plant
construction.
The higher the process temperatures
of power plants, the higher their
efficiency. So that pipelines can resist
the high temperature loads of 600°C and
more, high-temperature-resistant steels
such as T91 are increasingly being
used. In comparison to normal steels,
these have the required creep strength
to resist the loads through pressure and
flow values.
When forming these tubes it is vital to
take various aspects into consideration.
Due to the strength of these steels, the
bending machines used must have the
necessary bending forces. Yet despite
the strength, these materials react
more sensitively, and wall-thickness
tapering and out-of-roundness can
occur in the tube bend. It is, therefore,
essential that the tube bending machines
engaged for pipelines in power plant
construction meet the corresponding
tolerance specifications. These include,
for example, the European standard
EN 12952 or that of the American
Society of Mechanical Engineers ASME
B31.1. Meeting these standards plays a
significant role, in particular, in light of the
fact that power plant construction makes
increasing use of smaller boilers with
higher capacity. Heavier wall thicknesses
and smaller bending radii are required
to manufacture these high-performance
boilers. Not infrequently, the minimal
bending radius must be 1xD, depending
on tube diameter (in part also less than
1xD). In view of the high temperature-
resistant and sensitive materials,
the bending challenge behind this is
correspondingly significant.
Processes can be designed to be cost
efficient through efficiency increase,
not just in power plant operation. Lean
production processes already provide
an essential contribution towards cost
efficiency during the construction of
power plants. That is why machines
with two bend heads have established
themselves for the production of
pipelines, because they permit time-
optimised production of complex tube
serpentines.
The CNC 100 DB Twin by Schwarze-
Robitec represents such a solution.
It has two bend heads, which can be
moved vertically and horizontally (1x left
bending, 1x right bending) and which
bend the tube alternately clockwise
and anticlockwise. In this manner,
the machine offers high flexibility,
for example when manufacturing
superheater coils. The tube serpentine
does not need to be turned after each
bend, which guarantees quick and
economic production processes and the
manufacture of long side lengths. As an
option, both bend heads can also bend
in the same bending direction. By using
different sized bend formers, different
sized bending radii can be produced.
Especially conceptualised for power
plant construction, the CNC 100 DB Twin
also takes into consideration the initially
described properties of tubes made of
high-temperature-resistant steels. For a
Chinese power plant builder, for example,
Schwarze-Robitec designed both the
CNC 100 DB Twin and the customer-
specific bending tools according to
international standards. The power plant
builder produces boiler tubes made of
the high-temperature-resistant steels
with dimensions from 32 x 3.5 to 63.5 x
13mm.
Fully automatic manufacturing chains
make a further contribution towards cost
efficiency in power plant construction.
When storage, materials-handling and
manufacturing
technology
interact
optimally they reduce cycle times and
therefore decide about the performance
and competitive edge of a company.
Schwarze-Robitec
has
developed
an automation concept with which all
machines can be fitted with optional
extras, depending on bending order,
and expanded to a fully automatic
manufacturing system. Such a system on
the basis of the CNC 100 DBTwin has just
been delivered to the already mentioned
Chinese power plant construction
company. The rationalisation extends
across the complete production chain:
from material supply to handling and
quality testing all the way to the dispatch
of the ready bent pipelines.
The tube is moved via a transport
system from the warehouse to the
separating unit and is then conducted on
to the quality control of the weld seams.
After the X-ray control, the transport
system moves the flawless tube – the
faulty ones are rejected – to the other
end of the system. The transport trolley
with index head, which is mounted on
a hanging guide surface, takes over
the feed to the bending machine and
flip-over table. The flip-over table is
specially designed for handling the
long pipelines. The integrated flip-over
arms turn the tube serpentines quickly
and securely between the individual
bending procedures. During the bending
procedures, the flip-over arms position
themselves flat in rest position to avoid
collision with the serpentines.
Schwarze-Robitec GmbH
– Germany
Email:
sales@schwarze-robitec.comWebsite:
www.schwarze-robitec.comApplying bends effortlessly at the
rear end of a tube serpentine