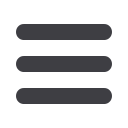

12
Electricity
+
Control
JULY 2017
Figure 6: Harmonic gearbox.
There are three parts:
• A cup shaped flexible spline with external
teeth which drives the auto output shaft
• A ring gear
• A driven wave generator
As the input shaft rotates, the wave generator ec-
centric action forces a portion of the spline into
mesh with the ring gear. Motion is imparted be-
cause the spline typically has two less teeth than
the ring gear. Each turn of the wave generator
moves the spline two teeth relative to the ring
gear. This process is analogous to a Vernier scale
where only one mark can line up at a time.
Output torque is high due to the relatively large
number of meshed teeth, and backlash is minimal.
This all comes at the expense of relativity high
friction and the need for special lubricants.
Figure 7
shows a slewing ring which usually
applied together with the harmonic gearbox. The
slewing ring imparts high rigidity in a compact
space and is seen, almost without exception, in
the joints of robotic articulated arm robots.
Figure 7: Slewing ring.
Matching motors and linear drive systems
Previous articles have touched on this subject in an
application specific way. A more systematic gener-
al approach follows.
Velocity, torque, power and inertia
These quantities define servo size and perfor-
mance. The speed reducer provides the interface
to the driven load and ensures that the correct mo-
tor size has been chosen.
Velocity
Maximum velocity of a motor is generally in the
range of 2 000 – 4 000 RPM (Revolution Per Min-
ute). In the case of
stepper motors
, maximum usa-
ble velocity is around 600 RPM.This is because de-
livered torque
decreases
with increased velocity.
Torque
Brushless servos have substantially constant torque
throughout their velocity range. Brushed servos are
not capable of simultaneous top speed and maxi-
mum torque. This constraint is due to high wear of
the brush gear.
Both of the foregoing motors are capable of
much greater peak torque for short periods. This
can be an advantage when the load only requires
high torque during acceleration or deceleration.
Resultant heating sets a time limit.
Peak torque in
stepper motors
should be re-
stricted to 60% of available torque. This is due to
the possibility of abrupt de-synchronisation of the
motor and consequent loss of commanded po-
sition. This is offset by the inherent much higher
torque delivery at speeds below 600 RPM, com-
pared to a servo motor.
Power
Power
is the product of
velocity
and
torque
. A
gearbox cannot increase motor power delivery. In
contrast to conventional wisdom,
power
is the last
parameter to be considered when sizing a system.
Inertia
Inertia is defined as the resistance of a body to any
change in its state of motion. The force required to
accelerate a body can be calculated from the body
mass and the required acceleration.
DRIVES, MOTORS + SWITCHGEAR