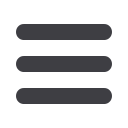

14
Electricity
+
Control
JULY 2017
T
hink about what happens when you switch
on your kettle in the morning. Apart from the
encouraging noises it makes, indicating that
coffee is not far away, all kinds of clever things are
going on inside the kettle’s electrical circuitry.
Every electric motor has a controller, and these
controllers differ in complexity and number of fea-
tures depending on the job they need to do. In
the case of your kettle, the controller is the on/off
switch, and you manually operate it so that your
kettle can perform its very important task.
Now imagine you had to make a thousand cups
of coffee, and needed to switch on 500 kettles all
at the same time. Not easy. In fact, pretty impos-
sible. This is why MCCs are such vital pieces of
equipment, controlling everything through a cen-
tralised system.
In its simplest application, an MCC is a panel
that works as a motor starter for several automat-
ed or semi-automated machines. Comprising one
or more enclosed sections with a common power
bus, an MCC can include variable frequency drives,
programmable controllers and metering. Essen-
tially, they are a type of electrical ‘filing cabinet,’
with ‘drawers’ full of lighting contactors, combina-
tion starters and other electrical control and distri-
bution products. Each section, or motor controller,
of the cabinet has a built-in safety mechanism to
protect the motor. These can be solid-state over-
load protection relays, fuses or a circuit breaker,
and there is usually a disconnecting switch as well
to isolate the motor circuit.
While they were first used in car manufactur-
ing, today MCCs are found in numerous commer-
cial and industrial applications, specifically where
there are multiple, remotely controlled loads linked
to a central control point.
Conclusion
Modern MCCs offer a host of benefits, including:
•
Reduced downtime:
Standardised sections
mean a simpler design, so operators require
less operational training. Plug-in units can be
easily swapped out for maintenance or re-
placement, and the inherent isolation of MCC
units means they can safely be serviced indi-
vidually, within legislated guidelines, without
switching off adjacent units
•
Quicker, cheaper installation:
MCCs have
their own factory-wired and tested units and
power buses, so field wiring and testing are
minimised
•
Flexibility:
MCCs can be easily expanded by
adding new units and sections
•
Space saving:
Much more compact than
mounting individual devices
JB Switchgear is known in the industry for de-
signing and manufacturing high quality switchgear
solutions that meet the latest national and interna-
tional safety and performance standards.
The company offers a comprehensive range of
fixed, de-mountable and withdrawable MCCs, so
talk to us about how we can help you get the solu-
tions you need.
Motor Control Centres
How They Work
Johan Basson, JB Switchgear
Motor Control Centres (MCCs) have been around since the 1950s when they were
first used by the car manufacturing industry, which needed many electric motors.
DRIVES, MOTORS + SWITCHGEAR
<<Author>>
Johan Basson is the
Managing Director of
JB Switchgear.
+27 (0) 11 027 5804 / +27 (0) 82 852 401
info@jbswitchgear.co.za www.jbswitchgear.co.zaAn MCC is a panel that
works as a motor starter
for several automated
or semi-automated ma-
chines.
An MCC can include Var-
iable Frequency Drives,
programmable control-
lers and metering.
MCCs control everything
through a centralised
system.
Take Note!
abbreviations
1
2
3
MCC
– Motor Control Centre
VFD
– Variable Frequency Drive
Essentially,
an MCC is a
type of filing
cabinet.