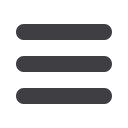

��������������������������������
������� ���� ���������� �����
�����������������������������
�������� ����� ��� ���� ��������
�������������������������
��������������������������
��������������������������
���� ������ ���� �����������
��������������������������
��������������������������
���������� ������������ ��� ��
���������������������������
���������������
�
Top-Performance-Emo-V5indd.indd 1
16.05.2011 17:09:56
www.read-tpt.comJ
uly
2011
115
›
Beam grinding work could be a thing of the past
HGG Profiling Contractors, a specialist
in 3D profiling, claims that its machines
can save 40% on welding and fitting time
compared to manual cutting; and 50% on
grinding time and 30% on machine time
compared to traditional beam profilers.
The company offers true automation from
design system to machine, compensation of
material deformation, and close-to-flange
cutting leaving less than 2mm of material
standing, almost completely removing the
need for grinding.
Plasma cutting the complete range
of beam sizes speeds up processing
compared with traditional oxyfuel cutting:
to cut a 48ft long beam W36x135 into three
parts, with both sides of each part having
beam-to-beam connection dressed with rat
holes, takes the RPC only 31 minutes. To
cut a 48ft long beam W18x40 into a single
part takes not more than 9 minutes.
Typical cuts in the offshore industry are
fixed/fully welded connections and pinned/
web welded connections. Both these
types of beam connections are cut leaving
material standing due to torch-material
distances. HGG’s cutting routines can deal
with this issue. While chamber cutting all
flange parts, the torch moves to inclined
positions allowing it to swipe part of the
web thickness away in the intersection of
web and flange.
This can only be achieved by having
full control over the robot path movements.
HGG has programmed specific robot control
software to allow direct control over every
single movement of the individual robot
axis (and the combinations of multiple axis
movement).
This allows the company to use the
above-described techniques involving
swiping, swinging and rotation of torches
to work in the close area of intersecting
web and flange parts, without colliding, and
without limitations.
With the flanges orientated sideways,
the top of the web is typically covered with
cutting residue. Special cutting routines are
developed to cut the top of the flanges from
the inside out, doing away with any slag
on the web, and also taking the radius into
account between flange and web.
All required operations on beam copes
are possible via the HGG beam profiling
software in collaboration with Tekla
Structures model, directly from the model,
without having to re-process the export data
from Tekla Structures.
At office level, NC information is created
directly from the Tekla Structures model for
the machine.
HGG provides an interface that makes
programming automatic, just by selection.
The result is that beams cut at the machine
level are not handled more than once (except
for minimal grinding for sharp edge removal).
The aim is to minimise or eliminate
manual intervention, so grinding more than
2mm would be unproductive. Anything
greater needs to be first cut by an expert
torch hand and then ground fine (triple
handling). This is why HGG’s cutting
routines keep all below 2mm.
HGG Profiling Contractors BV
–
The Netherlands
Email:
info@hgg.nlWebsite:
www.hgg-group.com