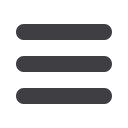

J
uly
2011
117
›
C
utting
, S
awing
& S
aw
B
lades
Orbital milling cut-off from Oto Mills
THE welded tube market continues to move
towards the production of very large and
thick tubes. For this industry Oto Mills
has developed the new cut-off model
TOAC40616, designed specifically for tube
lines that require cuts without burr on a wide
production range.
If just the thickness of the tube is to
be cut, a small diameter blade can be
used: this means greater rigidity, lower level
of vibrations and consequently improved
finishing and longer life of the blades.
The carriage consists of a steel structure
that supports the parts making up the
cut-off. It is driven by a pair of electric
motors with reduction gear that operate
just as many toothed pinions engaged in
turn with the rack on the bed. The outfeed
vice and the outfeed tube guide are fitted
on a mobile structure (vice detachment
carriage) that moves the tube away from
the blades as soon as the cut is completed
(with blades still inside the tube): in this
way they are protected against feasible
scraping/breakages if the tube should move
due to internal tensions or to the imperfect
alignment of the tube itself or even due to
synchronisation errors caused by excessive
oscillations in the line speed.
The bed also houses the mobile tube
supports: their stroke is based on the stroke
of the carriage and in particular, in view
of the type of connection of the cables to
the carriage, the support moves at half the
speed of the carriage, guaranteeing suitable
support of the tube throughout the cycle.
The cut-off houses the rotating part on
which the four cutting heads and relevant
oil-hydraulic clearance reduction cylinders
are fitted, which annul vibrations that could
possibly arise during the cutting phase.
The drives are installed at the back
end of the rotating part, protected from
chips and emulsion water, which rotate
the blades, as well as the relevant blade
traversing mechanisms (by means of linear
actuators) and the cable carrying chain.
The vices are designed so that,
within a specific shape (round or square/
rectangle) they are able to cover the whole
dimensional range of the machine without
having to re-tool. What’s more, the part of
the clamps that comes into contact with
the tube is lined with an insert in plastic
material to eliminate vibrations that could
arise during the cutting phases and also to
compensate any alignment anomalies of
the tube between the infeed and outfeed
vices.
The vice is the quick changeover type:
when you need to change profile (for
example from round to square/rectangle)
the whole vice is removed and replaced with
another vice offline, on which the clamps
suitable for the new profile to be cut are
fitted.
To ensure lasting life of the blades, the
cutting parameters used must be suitable
for the type of tube being produced (size,
thickness and material of the tube).
To help the operator in this choice and
to make it easier to enter these parameters,
the cut-off is equipped with dedicated
software (the cutoff manager).
When you enter the data of the tube
and the type of blade (HSS or TCT), the
program suggests the best tooth range. This
range is based on calculations that take into
consideration the shape of the contact
range and the filling of the compartment of
the teeth.
Oto Mills
– Italy
Website:
www.otomills.com