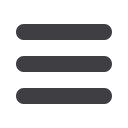

56
J
uly
2011
www.read-tpt.com›
T
echnology
U
pdate
THE pipeline industry is continuing to grow
worldwide to provide increased security of
energy and water supply, and with hostile
environmental conditions in many locations,
the pipeline protection market is expanding
to meet the requirements. Noru Tsalic,
Consultant at Applied Market Information,
has valued the pipe coating market at around
€5bn 2009 and predicts expansion to €6.5bn
by 2013. Tsalic was speaking at the February
2011 annual AMI conference on pipeline
coating in Vienna, Austria.
The highest demand for coatings is in
Asia with 23 per cent market share, followed
by Europe at 19 per cent, then NAFTA and
the CIS states at 17 per cent each. There
are a variety of different types of coatings
providing different functions: concrete is
the highest value sector at 42 per cent,
external anti-corrosion at 38 per cent, internal
coatings at 11 per cent and thermal insulation
at 9 per cent. Gas and oil use most of the
coated pipeline, with a small fraction in water
distribution. There is a newly developing
market for pipelines in carbon capture and
storage – the International Energy Agency
predicts the need for 43,000km by around
2030 for 1.44 Gt of carbon dioxide capture
per annum.
Europe currently imports 54 per cent
of its energy requirements each year, and
this will rise to 70% in 2030 as its resources
are depleted, according to Denso. This
is driving the push to build new pipelines
including Nord Stream, OPAL and NEL.
Europipe is supplying pipe, Max Streicher
GmbH is involved in construction and
Denso is carrying out field joint coating.
Nord Stream is around 1019km long and
will carry gas from Russia to Europe, where
the OPAL and NEL pipelines will connect
it to the existing network in Central and
Western Europe.
The basic external coating (by Mulheim
Pipe Coating) comprises fusion bonded
epoxy (FBE) primer, copolymer adhesive,
HDPE and finally a sintered PE rough
coat to prevent slipping. Much of this pipe
is also being coated with an outer heavy
concrete at two sites in Mukran and Kotka
by Eupec France. The owners of Nord
Stream are Gazprom (51%), Wintershall
(15.5%), Eon Ruhrgas (15.5%), Gas Unie
(9%) and GDF Suez (9%). Denso is using
a 2-tape self-amalgamating system for
field joint coating of the OPAL pipeline.
There are three main oil companies
in China: SinoPec and China National
Petroleum Corporation (CNPC)-PetroChina
onshore, and CNOOC offshore. At the
end of 2009 PetroChina operated around
29,000km of natural gas pipelines, 13,000km
of crude oil pipelines and around 9,000km
of oil products pipelines. In the 1950s China
constructed pipeline with asphalt coatings,
starting in 1958 with the first crude oil pipe in
Xinjiang. In the 1980s fusion bonded epoxy
(FBE) was introduced and liquid epoxy is
now also in use. Chief Engineer Liu Lingli of
PetroChina indicated that the contemporary
trend is for 3-layer polyethylene (PE) coating
on line pipe, and FBE at stations. Ageing
pipes that need recoating are generally given
a primary coating and wrapped in PE tape.
Applied Market Information Ltd
– UK
Email:
sh@amiplastics.comWebsite:
www.amiconferences.comImpact and anti-corrosion coatings for pipe