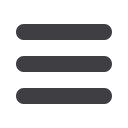

58
J
uly
2011
www.read-tpt.com›
T
echnology
U
pdate
BOSTON Matthews has launched a new
range of medium-speed ‘squeeze tube’
extrusion lines.
The medium-speed line forms part of a
range of extrusion lines designed by Boston
Matthews specifically for the production of
thin-walled polyethylene tubes used within
the packaging industry.
The capability to extrude a wide range of
tube sizes, configurations (1,2,3,4,5 layers)
and polymer blends and to quickly change
from one tube specification to another
allows the squeeze tube manufacturer to
react quickly in order to meet with the ever-
changing demands of their customers.
The new lines have been developed
by Boston Matthews through a close
association with a large number of squeeze
tube manufacturers from around the world
since the successful introduction of the
high-speed squeeze tube lines some six
years ago.
Observing that the ever-changing
consumer markets have placed greater
pressures and demands on tube makers to
manufacture a more diverse range of tube
sizes, specifications, blends and colours
Boston Matthews has reacted to this by
developing the medium speed line.
Boston Matthews sales director Simon
Brookes said: “We are always listening to
our customers and constantly monitoring
market trends. This enables us to develop
and design our equipment to meet with
the specific requirements and demands of
today’s markets and also for the future.”
The medium speed line has been
extremely well received by tube
manufacturers around the world with
orders successfully completed and in full
production within several of the industry’s
leading tube producers. Interest at the
K’2010 was also very high with tube
manufacturers specifically visiting the
Boston Matthews stand to discuss their
extrusion requirements.
Flexibility and the importance of quick
change-over have been designed into every
element of the line. The die head has the
ability to change colour or polymer faster; to
produce different tube layer configurations
without adjustment; simple disassembly on
the extrusion line eliminating the need for
heavy lifting equipment; and shorter flow
passages for higher quality production.
The die head incorporates a combination
of technologies to ensure the successful
processing of the wide range of blends,
masterbatches and additives associated with
squeeze tube production takes place in order
to achieve the extremely high standard of
surface finish which is essential for the tube
decorating operation.
These advancements in die head
technology are in combination with the
development of calibration, cooling and
cutting technologies that provide the
processor with more flexibility whilst making
improvements in production quality.
The tube calibration system has been
designed for easy, damage-free removal
incorporating quick and easy size change
and also for quick and easy cleaning when
required. The unit is designed in such as
way so that identification of a tube scratch/
contamination issue can be quickly identified
and recertified without involving heavy lifting
equipment, which can potentially cause
further damage.
Diameter monitoring, automatic tube
rejection systems and complete line control
ensure that tube production quality is
constantly maintained and that the medium-
speed extrusion line can be easily integrated
within a fully automated tube manufacturing
facility.
Line control and operation is made
simple and easy via the Smart 15"
colour touch-screen operating system.
Features include automatic line start-up;
recipe storage; constant performance
monitoring and diagnostics, language
selection, process data access, and
password protection. Security levels can
be customised to ensure settings cannot
be changed without the proper permission:
very useful for night shifts. Ethernet
connectivity can allow the line to be added
to a computer network for production data
storage, access and remote monitoring.
Simon Brookes said: “For many years
now there has been talk about accessing
and manipulating production data but now
it is a reality. More and more of our
customers are using the Smart System not
only as an extrusion control system but
as an effective production monitoring and
quality control tool.”
Boston Matthews
– UK
Email:
sales@bostonmatthews.co.ukWebsite:
www.bostonmatthews.comThe medium-speed squeeze tube extrusion line
Flexible extrusion lines for squeeze tubes