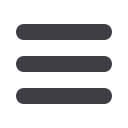

Global Marketplace
www.read-tpt.comN
ovember
2015
67
that. According to the researchers at Massachusetts Institute
of Technology (MIT) who developed the method, graphene
coatings have, unlike polymer coatings, proved in laboratory
tests to be highly durable.
The discovery could be important for the energy industry
worldwide. Most power plants – whether they utilise coal,
natural gas or nuclear fission – make electricity by generating
steam that turns a turbine. That steam is condensed back to
water, and the cycle begins again. But the MIT researchers
assert that the condensers that collect the steam are quite
inefficient.
Professors Evelyn Wang and Jing Kong, graduate student
Daniel Preston, and their teammates believe that the
improvement they achieved in condenser heat transfer could
lead to an overall improvement in power plant efficiency of
two to three per cent. Mr Preston said that this is sufficient to
make a significant dent in global carbon emissions.
Citing data from the Electric Power Research Institute (Palo
Alto, California), he told
R&D
, “That translates into millions of
dollars per power plant per year.”
The goal of much research has been to enhance droplet
formation on the surface of condensers – coiled metal tubes,
often made of copper – by making them water-repellent. The
fragility of polymer coatings in the heat and humidity of power
plants led the MIT colleagues to consider graphene, known to
be hydrophobic by nature.
›
Mr Preston said that, because the graphene coating
process – chemical vapour deposition – has already
been tested extensively, the new method could be ready for
testing under real-world conditions “in as little as a year.” In
his view the process should readily adapt to power plant-sized
condenser coils.
Automotive
German automaker Daimler
implements a winning idea
for a shuttered Hummer plant
in Indiana: turning out luxury
Mercedes-Benz SUVs for China
exclusively
The steady comeback of the US auto industry has revived
underused factories across the country as carmakers strive
to meet growing demand. But, as noted by Bill Vlasic of the
New York Times
, in this industry on the rebound the revival
of one particular idled plant – in Mishawaka, in northern
Indiana – stands out. This past summer, AM General – the
maker of Humvee military vehicles – commenced production
of a Mercedes-Benz sport utility vehicle in a sprawling factory
that once built Hummer SUVs for General Motors. The plant
ground to a halt when GM went bankrupt in 2009, shutting
down the Hummer brand as a condition of a $49 billion
government bailout.
Now the old Hummer plant has been resurrected and AM
General’s hourly workers – members of the oldest United
Automobile Workers (UAW) local in the nation – are building
German luxury SUVs for a specific clientele: consumers
in China. In the process, wrote Mr Vlasic, the US factory
believed to be one of a kind in shipping its entire output for
sale in the Chinese market “has become an example of how
a modest-size Rust Belt manufacturer can find its niche in an
increasingly global automotive industry.” (“In Former Hummer
Plant in Indiana, Mercedes Turns Out SUVs for China,”
11 August)
As recounted by Mr Vlasic, theAMGeneral plant was only eight
years old when GM went bankrupt. Some 1,000 workers were
laid off. The plant started its slow recovery in 2011, building a
van for handicapped people for the start-up company MV-1.
But production was too small to warrant recalling very many of
AM General’s workers. And its plant was considerably larger
than required for making just the MV-1 van.
T
he
R-
class
and
the
C
hina
connection
At this point, as the auto industry in the US was beginning to
stir, fortune was also about to favour AM General. The German
automaker Daimler, parent company of Mercedes-Benz, was
running short on production capacity for SUVs at its factory
in Alabama. Mercedes officials in 2014 started scouting other
sites for one of their models, the R-class.
The major variable in the equation fell into place. Mr Vlasic
wrote: “The R-class had never caught on with American
consumers, and sales in the United States were discontinued
a few years ago. But the sleek, station-wagon-shaped model
was a hit in China, and Mercedes was determined to keep
building it.”
Jason Hoff, the head of Mercedes operations in the United
States, deemed it impractical to relocate the supply base for
the R-class from North America to China. That would have
been far too expensive, he told Mr Vlasic.
Instead, Mercedes signed a multi-year contract to have AM
General assemble the R-class in Mishawaka, using parts
shipped into the facility from suppliers throughout North
America and Europe. Now, the plant is building between 70
and 100 vehicles a day, mostly R-class SUVs as well as a
small number of MV-1 vans.
“They had a lot of experience here and a very good work
force,” Mr Hoff said. “And the facility is very flexible and can
integrate our product quite well.”
For another distinguishing feature of the Mishawaka story, an
AM General spokesman said that the company did not need
any financial incentives from state or local government to
retool the plant for the new model.
›
Bernard Swiecki, of the Center for Automotive Research,
told the
Times
that the Mercedes-Benz initiative was a sign
of an industry with the wind at its back. The centre estimates
that, in 2010 and into 2011, capacity utilisation at auto plants
in North America – the US, Canada and Mexico – had fallen
to about 70 per cent. In 2012, when the economic recovery
began, that rose to 91 per cent. In 2014 it grew to 96 per cent.