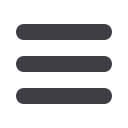

Tube mi l ls & rol l forming l ines
www.read-tpt.comN
ovember
2015
71
Latest developments for ten-roll
straighteners
THE Asmag Group is a supplier of
machinery and equipment for the steel
and stainless steel tube industry. It
combines two companies – Asmag,
founded 1984 and located in Austria,
which focuses on the design and
manufacture of drawing, straightening,
testing, cutting, chamfering, stacking
and bundling machines, and Seuthe,
which was founded in 1899 and located
in Germany and has its core business in
the design and manufacture of tube and
rollforming mills.
With more than 200 employees, the
Asmag Group has the capability of
designing and manufacturing complete
tube welding lines from sheet coil to
ready-to-sell tube bundles.
The group’s latest project is the
installation of two complete straightening
and testing lines for a European
producer of stainless steel tubes. The
larger of the two machines is designed
for a diameter of up to 50mm, and the
smaller for a diameter of up to 30mm.
To eliminate crane waiting times,
double troughs are provided in both
the tube bundle delivery and tube
bundle removal. Downstream from
the bundle loading device, the tubes
are automatically separated, and are
cleaned on the outer surface upstream
of the straightener.
The key machines of the plants are
the ten-roll straighteners of the RRM
pro series. The features of this series
are the backlash-free hydraulic height
adjustment drives in all ten straightening
rolls, the individual drives in the
straightening rolls, a straightening force
display on each straightening roll, and
computer-supported machine setting.
In addition to the fully automatic
operation of the plants, the newly
developed straightening roll cleaning
device contributes to thehighproductivity
of the machines. The straightening rolls
are cleaned automatically in cycles
using polishing rollers without any
manual intervention.
To meet the high quality requirements,
all tubes are measured for straightness
directly after leaving the straightener.
Depending on customer requirements,
the permissible tolerances can be freely
specified on an HMI. A sorting device,
which uses X-ray technology, prevents
incorrect materials from reaching the
order batch.
The tubes are subsequently eddy
current tested at the end of the plant and
measured using multi-axis lasers.
Asmag GmbH
– Austria
Email:
sales@asmag.atWebsite:
www.asmag.atNew rollform line coil end welders
KENT Corporation has introduced
a new coil end welder for press and
rollform lines. The new line of welders
offers a manual or air shear, air clamps
and automatic TIG weld.
The machines are portable for use on
more than one line. Designs range from
7" to 18" wide. Eliminating rethreading
rollform and press lines reduces coil
change downtime, scrap and tooling
damage.
The new machine will be on display
at the FABTECH Chicago show,
on booth S4975. Kent can provide
cost justification work sheets and
articles, and will carry out a complete
cost justification for users at no
charge.
The company offers a full line of coil
end welders up to 96" wide, as well
as coil handling and feeding, and a
complete line of tube mill products.
Kent has been providing quality
entry equipment, strip end welders,
accumulators, high-speed cold saws
and tube mill consumables to the tube
mill, rollforming and stamping industry
for more than 40 years. The company
has delivered more than 6,000 pieces
of equipment that are currently running
successfully, with applications that vary
from 0.2 to 19mm thick (0.008" to 0.75"),
and from strip widths of 12.7mm to over
2,032mm (0.5" to 80").
Kent Corp
– USA
Fax: +1 440 582 9654
Email:
sales@kenttesgo.comWebsite:
www.kenttesgo.comReducing downtime while cutting
on your tube mill
RANDOLPH Tool’s vertical and
horizontal tube cut-off blades, as well as
jaws/dies, are manufactured with highly
specialised tooling processes, by expert
craftsmen.
The blades are extremely flat and
smooth, which causes less friction
during the cutting process. This, in
turn, helps the blades to last longer,
which means less downtime and
more production. The blades lasting
significantly longer will also reflect on
your bottom line with fewer dollars
spent at the end of the year.
Randolph Tool is also recognised
widely for its engineering capabilities,
management excellence and consulta-
tion services. By collaborating with its
customers from start to finish it aims to
help them to maximise their potential.
Randolph Tool Co Inc
– USA
Email:
info@randolphtool.comWebsite:
www.randolphtool.com