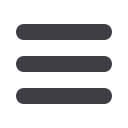

Tube mi l ls & rol l forming l ines
www.read-tpt.com72
N
ovember
2015
Formtek completes upgrade to
in-house laser welding tube mill
A MANUFACTURER of bathroom
fixtures and fittings has found an answer
to its production challenges in the form of
the Yoder QVW-150 fibre laser tube mill.
The US manufacturer had been
relying on outside vendors to produce
the tubing using the conventional TIG
welding method, but found that the cost
and labour was not in line with target
production goals. The customer turned to
Formtek’s solution engineers for a better
answer to its needs.
Brian Kopack, the Formtek engineer
working with the client, said: “Formtek
was chosen due to its innovative methods
for working with laser technologies,
specifically with the fibre laser welding
process in this case. That welding
technique is integrated into our QVW-150
machine. They really valued the ability to
invest in their own tube-manufacturing
and meet higher volume goals, and so
we found a way to deliver that for them.”
From end-to-end, the QVW-150 fibre
laser tube mill serves as a complete
solution for manufacturing the stainless
steel tubing required for the customer’s
products. Starting with the coiled raw
stainless steel material, the mill creates
tubing with a diameter of 0.5" to 1.5"
and wall thickness of 0.025" to 0.045".
Tubing is formed using conventional
methods, then laser-welded using the
proper FDA safety specifications.
Post-processing is also performed,
starting with the OD weld bead being
removed to customer specifications,
followed by cutting the tube as
programmed by the customer, and
ending with de-burring using a brushing
system and transferring to a three-station
OD polishing system, complete with dust
collection. A coolant filtration system is
used for forming and sizing machines to
ensure the longest possible roll tooling
life and minimal amounts of tube marking.
Mr Kopack elaborated on the project:
“The QVW-150 machine was the ideal
fit for the customer’s project needs. The
fibre laser welding process significantly
increases production speed compared
to the TIG welding process that was
used by their vendors.
“It also enables them to work
with a more ductile weld area and
a decreased heat affected zone –
something crucial to their products,
which often have tight bending radii.
The additional processing steps that
were consolidated into the design really
allowed the customer to produce the
higher capacity they needed without
investing in a second machine, keeping
costs low and revenue high.”
Formtek, Inc
– USA
Fax: +1 216 292 2898
Email:
sales@formtekgroup.comWebsite:
www.formtekgroup.comMetal sheet rollforming machines
SEN Fung Rollform Machinery Corp
is recognised as one of the leading
suppliers of metal sheet rollforming
machines in Taiwan. With more than 50
years of experience, the company offers
quality, durable and customer-orientated
facilities worldwide.
Sen Fung is capable of manufacturing
high-speed and automated machinery
by constantly engaging in innovation.
It has been responsible for numerous
inventions which are used and patented
in many different countries. The
company’s service team also prides
itself on its accurate worldwide after-
sales service to customers.
Sen Fung Rollform Machinery Corp
–
China
Email:
service@senfung.comWebsite:
www.senfung.comOne-stop resource for tube, pipe
and rollform machinery
UNIVERSAL Tube & Rollform has
the knowledge to offer a complete
turnkey system, from the initial design
to start-up. Located under one roof
with Universal Controls Group, a
rapidly growing controls supplier, the
companies’ relationship enables them
to offer a wide array of services.
An extensive inventory of used and
reconditioned machinery is available,
as well as line upgrades and repower
systems, and full import and export
services. The company can offer cash
for surplus machinery, and also provides
new drive systems, components and
accessories.
Universal
Tube
&
Rollform’s
125,000ft
2
warehouse is fully stocked
and ready for hands-on inspection of the
equipment. Different types of tube mills
or rollformers are available to fit specific
needs. The company’s experienced
team will assemble a complete line
quotation based on a faxed or emailed
drawing of the shape to be fabricated.
Universal will be at FABTECHChicago,
9-12 November, at booth N6010.
Universal Tube & Rollform Equipment
Corp
– USA
Fax: +1 419 874 2825
Email:
sales@utubeonline.comWebsite:
www.utubeonline.com