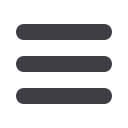

Tube mi l ls & rol l forming l ines
www.read-tpt.com76
N
ovember
2015
New standards in milling
stainless steel
STAINLESS steel is a challenging
material for milling machines. It
readily clogs the cutting tool due to
its toughness. The varying chemical
compositions and mechanical properties
of the individual types of stainless steel
require completely different cutting and
tension parameters to non-alloy steels,
and the maximum processing speed
is correspondingly lower. Efficient
machining of stainless steels therefore
poses a significant challenge.
Linsinger, an Austrian manufacturer
of special-purpose machines, has taken
on this challenge. The first stainless
steel plate edge milling machine has
been successfully in use since 2011 at
the premises of a producer of stainless
steel pipes. In the longitudinal welding
process, pipes for the natural gas and oil
industry are manufactured.
A further three plate edge milling
machines for stainless steel have
been designed and built according
to customer requirements, and are in
operation.
The machine from the Linsinger PFM
series ensures the optimum preparation
of the welding seams on the two long
sides of the stainless steel plates. The
machine has a vertical plate waviness
tracking function, and the milling units
work over the whole plate length with
high precision. They allow the whole
milling profile to be produced in a
single working step on both long sides
at the same time. This is an important
advantage for perfect welding, which
should ideally be produced in one step.
The cutter head must be replaced only
when changing to a different profile, and
this exchange can also be automated.
Another advantage of the PFM is its
flexibility. All parameters can be adapted
to the different types of stainless steels.
As the machine measures each plate
separately, even the smallest batch sizes
can be produced efficiently. Linsinger
has also developed specific, multi-layer
coated and particularly resistant carbide
inserts with special cutting geometries
for a wide range of stainless steels.
Linsinger Maschinenbau GmbH
–
Austria
Fax: +43 7613 8840 951
Email:
maschinenbau@linsinger.comWebsite:
www.linsinger.comStainless steel plate edge milling technology from Linsinger
Is rollforming a bending method?
AS defined, rollforming is a pure
bending method. On the shop floor,
however, additional massive forming
often occurs, sometimes desirably, but
often not. This can hardly be avoided,
if a hem should be folded at the sheet
edge with a few roll stands only.
Other applications include desired
sheet thickness modifications such
as forming a notch into the sheet or
forming outer radii that are smaller than
the sheet thickness.
Deep drawing effects often occur
undesirably, eg if two or more bending
zones on one profile side are formed
at the same time and the sheet edges
are prevented from ‘flowing’ into the roll
stand.
The designer wants to have a reliable
prediction about the result of these
effects. For this, finite element analysis
(FEA) is particularly suitable. In doing
so, shell and solid elements can be
selected.
Shell elements are suited to pure
bending; the calculation is quick
and effective. However, limits exist
if massive forming occurs. In this
case solid elements are better. The
calculation, however, needs more time
to be completed.
In the new release of the roll form
design software UBECO Profil, the
designer can select between shell
and solid elements, dependent on the
application. The software creates the
simulation model for the FEA system
LS-DYNA automatically. In the case
of a solid model, selection among two,
four, six or more elements in sheet
thickness direction is possible.
These and more new functions will
be shown at the Blechexpo exhibition,
3-6 November, in Stuttgart, Germany
– Hall 7, Stand 7508 (EFB joint stand).
The FEA system LS-DYNA will be at the
same stand, presented by DYNAmore.
The new release will be available from
December 2015.
UBECO GmbH
– Germany
Fax: +49 2371 45550
Email:
info@ubeco.comWebsite:
www.ubeco.com