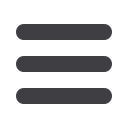

wire
2014
- New products on show
April 7
th
– 11
th
78
wire
2014
Upcast OY
Stand: 09C06
The original Upcast continuous casting
technology allows casting of top quality
copper and copper alloy rod in the most
cost efficient way.
It is a simple process with easy operation
through an advanced control system, with
reliability built on 40 years of consistent
development work, operational experience
and excellent customer service.
There is a wide range of alloyed coppers
and copper alloys that can be cast with
Upcast. These include, as an example,
silver bearing and phosphor-deoxidised
coppers, brasses and bronzes; copper
magnesium may soon become part of the
range.
As new applications for copper alloys are
being developed and new types of copper
alloys emerge, the utilisation of Upcast
technology within the copper alloys field is
rapidly increasing.
Upcast rod production lines are of modular
design. Both single and double-furnace
configurations are possible. With a
double-furnace configuration – having
separate melting and casting furnaces – it
is possible to reach 40,000tpa output, while
12,000tpa is possible for a single-furnace
configuration.
Different rod sizes can be cast
simultaneously and the output and product
mix can be adjusted. Upcast lines are
extremely flexible and tailor-made to match
the needs of each specific customer.
If scrap – clean and dry – forms a
significant part of the input material then
a double-furnace configuration should be
the preferred choice.
The majority of delivered Upcast lines are
for Cu-OF rod. The most common cast rod
diameter is 8mm which is the standard size
within the cable and wire industry.
Rods with bigger diameters are used for
manufacturing a variety of products eg
bus-bars, trolley wires, electroplating
anodes etc. Upcast Cu-OF rod is
well-suited for all electrical applications and
has become the preferred feedstock
especially for:
• fine and multi-wire drawing where
ductility requirements are most
demanding
• enamel wire production where surface
finish is of utmost importance
• continuous rotary extrusion where tool
wear rate is a crucial factor
Absence of harmful emissions and need for
waste treatment reduces the environmental
footprint of Upcast casting lines.
In addition to the small environmental
footprint other Upcast GREENerCAST
characteristics are clear: low lifecycle
costs, easy variation of output, use of scrap
in the process and unique upgradability.
Upcast OY – Finland
Website
:
www.upcast.comWTM Srl
Stand: 11E77
WTM will show all visitors the results of its
most recent research. Inspired by the
direct experience and the production
needs of customers, new solutions have
been developed by its engineers for
enhancing the production performance and
possibilities of its taping equipment.
In particular, on display will be:
• A working horizontal line with twotaping
modules wrapping polyimide +PTFE,
typical application for aerospace
cables. They will be equipped with new
150mm and 200mm taping heads for
cross wound spools, that can run up to
3,000rpm, fitted with a high sensitivity
tape tension control.
These heads are also suitable for any
other kind of tape. For the quality
control on the taping process, the Visio
System will be installed and working.
• A working vertical taping line suitable
for a revolutionary mica tape, an
innovative tape for the production of
fire resistant and fire retardant cables.
The advantages of this new technology
are no tape-flicking effect, reduced
quantity of tape needed, increased
production efficiency in the following
extrusion
process
and
smaller
thickness of the required external
insulating material; all this resulting in a
greater efficiency in the cable
installation. The line is completed with
translating take-up and pay-off,
allowing reduced footprint.
In addition to these machines, WTM will
illustrate a new line developed for the
application of metallic tapes on coaxial
cables suitable for high frequencies, and all
its production range, together with taping
lines for other applications. These include
single twist bunching machines, sintering
ovens, and machines for testing cables etc.
WTM Srl – Italy
Website
:
www.wtmachinery.comZumbach
Stand: 11D43
❍
Cost efficient solution from Upcast
Novel, intelligent and cost-efficient
solutions for in-line measurement and
control of wires and cables are going to be
the focus of Zumbach’s stand at wire 2014.
New linear sensor technology allows
cost-effective, synchronous multi-axis
measurement of diameter and ovality in any
cable, tube and hose extrusion process.
Unique measurement technology for
products up to 200mm outside diameter:
• A new product line with two-coloured
LED
light
sources
allowing
simultaneous scanning in each axis
(XY) and thus trouble-free measurement
even with product vibration. This new
concept allows even a four-axis
measurement of products up to 54mm
diameter
• Integrated extraneous light filters
prevent occurrence of measurement
errors that to date seemed unavoidable
• Perfect performance even with
reflective surfaces thanks to the use of
different colour lighting for each
measurement axis
The high-tech ultrasonic system Wallmaster
offers application-specific solutions for
measuring and monitoring wall thickness.
The measuring data processor with
touch-screen display gathers data and fully
automatic quality control.
In combination with ultrasonic UMAC
®
scanners and various ODAC
®
diameter
measuring gauges as well as error
detectors, the measuring and monitoring
scale can be expanded to outside and
inside diameter, statistics, SPC and
processor communication.
Using Zumbach’s Wallmaster measurement
and control systems, manufacturers can
economise their expenditure of raw
materials. The novel construction (patent
pending) of new ultrasonic scanners is
going to be a highlight: the transducers can
be either individually or simultaneously
adjusted to the best possible measuring
position within seconds. The scanners
cover an outside diameter up to 180mm
and represent a smart and simple solution
for full non-contact, in-line eccentricity and
wall thickness measurement of cable
jackets, tubes and hoses.
Zumbach Electronic AG – Switzerland
Website
:
www.zumbach.com