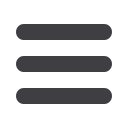

Technology News
www.read-tpt.com38
J
anuary
2013
Versatile and powerful pipe
bending solution
PINES Technology, an Ohio, USA
-based manufacturer of pipe bending
machinery, has recently shipped a No.
6 heavy duty rotary hydraulic bending
machine to Morris Coupling for its
Knoxville, USA facility.
Morris Coupling is a world leader in
the manufacture of bent components
for pneumatic conveying systems,
high-performance exhaust systems,
heat exchangers and other industrial
products. Morris chose the Pines
No. 6 to achieve its high output goals
and maintain standards of quality. Its
products include short and long radius
bends ranging in size from 1½" to 8"
OD and bend radii from 2½" through to
approximately 72".
The Pines No. 6 is a powerful and
dependable work-horse that offers fast
set-up and changeover advantages. It
is equipped with a Pines “Dial-A-Bend”
SE PLC control delivering a high level
of performance, precision and flexibility.
The control stores up to 1,000 different
bending programs.
Offering high production of multiple
bend parts, the No. 6 is capable of fast,
repeatable bending of pipe and tubing
up to 8" OD. Wall thicknesses vary with
different materials.
The machine has clockwise rotation,
electric solenoid-actuated hydraulic
circuit controlled from a convenient push
button operating station and cushioned
hydraulic cylinders to eliminate shock
and extend machine life. The machine is
fitted with a special, long stroke mandrel
extractor that has electric tangent and
CLR (centre line radius) adjustment. Ian
Williamson, Pines CEO, said: “Both Pines
and Morris Coupling are great American
companies that have been in business
for nearly 70 years. I look forward to a
long, mutually rewarding relationship
with Morris Coupling.”
Pines Technology
– USA
Website:
www.pinestech.comServo motor driven tube machine
from Haven Manufacturing
HAVEN Manufacturing, a designer
and producer of tube and bar cutting
machines, has introduced the latest
addition to its product line. The Haven
Model 873 servo tube re-cut machine
enables manufacturers to cut round,
square and rectangular tubing to a
variety of precise lengths, quickly and
automatically.
By feeding the material to be cut
through the integrated servo motor
controlled linear slide, the Haven
machine is able to be pre-programmed
by the operator to cut multiple length and
quantity parts from each individual mill
length tube, maximising material use and
minimising both wasted time and money.
The cut-off process begins when mill
length tube bundles up to 30" in diameter
are placed into the integrated loader/un-
scrambler by overhead hoist or forklift.
The tubes are then gently lifted by five
elevating slings to load position, where
single tubes gravity feed onto an inclined
table that controls the feed rate into the
re-cut machine.
As each individual tube reaches
loading position, it feeds into v-rollers
and is ready to advance towards the
Haven cutting head. At this point the
tube is gripped by a set of slide clamps
controlled by the highly precise integrated
servo motor and is moved forward into
the now-open dual-blade cut-off head
to the exact length required. The Model
#873 uses the same dual-blade, shear
tube recut technology utilised in Haven
tube re-cut machines for over 30 years.
As the tube is being cut, the slide
clamp retracts to its original position and
is ready to advance the tube to the next
pre-programmed cutting length. The
Model #873 accomplishes the shearing
process in fractions of a second and the
system can achieve up to 3,000 cycles
per hour.
Haven Manufacturing
– USA
Email:
info@havencut.comWebsite:
www.havencut.comHaven’s Model 873 servo tube
re-cut machine
Morris Coupling’s
new Pines Standard
Model No. 6, Series
116 bender