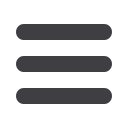

Technology News
www.read-tpt.comJ
anuary
2013
39
Welding with arc voltage control
ALTERNATING current (AC) welding of
aluminium and its alloys with arc voltage
control (AVC) using the Polysoude
PC 350 AC/DC controller and Tetrix 351
source is now possible thanks to a
collaboration
between
Polysoude
(concerning AVC regulation) and EWM
(concerning source regulation).
The main obstacle with aluminium
AC welding is the AVC regulation which
does not support any phase jumps.
The availability of the AVC function in
AC gives Polysoude great competitive
advantage.
The word “aluminium” is only a generic
term used to describe, apart from pure
aluminium, the entire range of alloys
which the majority of applications are
composed of. Orbital welding of tubing
systems and pipelines in aluminium
alloy prove to be particularly interesting
in the case of cryogenic and nuclear
applications, which require a high level of
quality. The advantages of an automatic
weld process lie in the traceability and
the replication of parameters linked to the
electronic control of power sources. This
replication allows for the creation of an
elaborated welding procedure resulting
in constant high quality welds.
In 90 per cent of all cases appearance
of H2 is caused by contaminated surfaces
or humidity absorbed by the oxide layer.
In some cases H2 comes from the base
material or the filler wire.
Recommendations: using exclusively
clean and dry materials; thorough
protection of filler wire against any
contamination; milling of zones to be
welded; good shielding gas cover;
and preheating of workpieces (at a
temperature of 100°C).
AC current is used essentially for the
welding of aluminium and its alloys. InAC
mode, the tungsten electrode is switched
between positive polarity (acting as a
cathode) and negative polarity (acting as
an anode). During positive polarity with
the electrode as a cathode the oxide
layer on the surface of the workpiece is
destroyed (cleaning sequence). During
negative polarity with the electrode as
anode the heat necessary to melt the
material is transferred to the workpiece,
the temperature of the electrode can
decrease during this time (penetration
sequence).
Polysoude
– France
Email:
info@polysoude.comWebsite:
www.polysoude.com