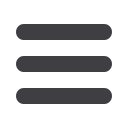

62
J
anuary
2013
Technology News
Weld-Tech ApS
Email:
weld-tech@weld-tech.comTel: +45 46194647
Need tools
for Pipe
Welding?
Manufacturing
Distribution
Meet us
in Essen 2013
Hall 8 Booth B139
... Contact us
www.weld-tech.comDescaling 14 tons of
steel bars in one hour
DRAWN steel, also known as bright
steel, used in the production of injection
parts for diesel engines, must meet
strict quality standards. A key stage in
the manufacturing of drawn bright steel
is the blast cleaning of the raw material
prior to the drawing process. Recently,
Rösler developed a continuous shot
blast system for a leading manufacturer
allowing the fully automatic blast
cleaning of steel bars with diameters/
cross-sectional dimensions of 24 to
80mm (approximately 1.0 – 3.2"). This
system not only produces excellent
descaling results but permits processing
speeds of up to 60m (197ft) per minute.
As a fully owned subsidiary of
Saarstahl AG, Saar-Blankstahl GmbH
is able to procure all its raw steel
requirements from the parent company.
This is a key factor for the quality of the
Saar-Blankstahl drawn steel products
sold all over the world. Other factors
for the high quality of these products
are the comprehensive know-how and
state-of-the-art manufacturing lines
for the drawing, peeling/stripping and
heat treatment processes. In addition,
the company, with plants in Homburg
and Burbach, can offer in-house high
performance quality control technologies
like eddy current and ultra sonic testing.
By
individually
planning
and
coordinating
the
manufacturing
processes and using special wires and
steel bars, Saar-Blankstahl can produce
high performance steel products for
the most challenging applications, for
example, in the automotive industry.
Prior to being drawn into steel bars
with standard round, square and
hexagonal profiles as well as steel
bars with special profiles, the rolled
steel must be blast cleaned to remove
scale and rust from its surface. Günther
Dorscheid, plant manager at Saar-
Blankstahl, said: “Blast cleaning is
highly critical for meeting the specific
customer requirements for an absolutely
homogeneous surface, for two reasons:
on the one hand, residual scale on
the steel can damage the drawing die,
which causes scratch marks on the
drawn steel products. And on the other
hand, scale embedded in the drawn
steel can damage the tools during the
subsequent machining process. For this
reason, after the blast cleaning process
the surface of the rolled steel must have
a degree of cleanliness of SA 2.5 –
SA 3.” This was a key requirement for
the replacement of the old shot blast
machine with a new blast cleaning
system in the Burbach plant. In addition,
the customer specifications called for a
high parts throughput, high equipment
availability, ease of maintenance and a
highly efficient dust collection system.
Rösler Oberflächentechnik GmbH
–
Germany
Fax: +49 95339 24300
Email:
b.mueller@rosler.comWebsite:
www.rosler.comCleaning steel bars with diameters up to 80mm