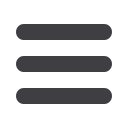

Coi l ing
and
uncoi l ing machinery
www.read-tpt.comJ
anuary
2013
93
Tube coiling: low or high
production speeds, small
or large diameters
AS with any machine that is introduced
to a processing line, a tube coiler
needs to be properly sized and have
the necessary features to meet the
needs of the application. Items such as
passline, processing speed, diameter
size and coiling diameter all play a role
in how the tube coiler is arranged and
designed.
Many tube coilers are designed
with a specific market focus, such as
automotive brake line, automotive fuel
line, welding wire and wire products or
energy-based pipe products.
Tube coilers are not limited to smaller
diameter tubes, such as 12.7mm (0.5");
there are tube coilers that can coil pipe
products up to 88.9mm OD x 6.4mm
wall thickness (3.5" x 0.25").
Several types of tube coiler are on
the market and all have their respective
advantages. There are tube coilers that
orientate their coils horizontally and
vertically, tube coilers that process only
one coil at a time with a slow change
of spools, and coilers that have quick
change spools, so no production is lost
or slowed.
Production speeds can dictate special
characteristics such as coil holders that
act like tube coil accumulators to allow
the tube coil holders to change spools
without stopping production. The
method of switching tube coil holders
is also dependent on production
speeds: low speeds can typically be
accomplished by hydraulic motion
control methods with one or two
holders, while high speeds tend to
require electric motion control methods
with two or three holders.
More advanced tube coilers have
built in cut-offs so as to index the tube
to the next empty spool without any
assistance from the operator. The
automation takes care of cutting the
tube, holding a few coil wraps while the
system is switching tube coil holders
from a full to an empty unit. Tube coilers
are an acceptable alternative to inline
tube cutting. They must be designed
properly so as not to be a bottleneck
in processes and a variety of styles
and options exist to fulfil the desired
production goals.
Formtek, Inc
– USA
Fax: +1 216 292 2898
Website:
www.formtekgroup.comRedefining the installation of
large diameter HDPE pipe
LOW Ovality technology from Pipe Coil
Technology Limited (PCT) allows large
diameter HDPE pipe up to DN315 to be
coiled as free standing coils or reeled
onto drums. This innovative technology
has been used in Europe for many
years now and is rapidly increasing in
popularity worldwide due to the many
advantages it offers. There are still
many pipe manufacturers that continue
to manufacture large diameter HDPE in
the traditional 12 or 20m ‘stick’ lengths
regardless of its final use. This is not only
highly inefficient to store and transport
but also drastically decreases the overall
integrity of the installed pipeline as butt
welded and electro fusion joints are still
the most common inherent failure in a
pipe designed to last 100 years.
Low Ovality Technology not only
reduces transport costs by maximising
the amount of coiled pipe per load but
also greatly increases the integrity of the
finished pipeline. For example, DN160
pipe can be coiled in 900m lengths
allowing for a much quicker installation
time by removing up to 73 butt welds
per 900m coil, and with less joints
the pipeline’s integrity is significantly
increased. For larger projects, 4,600m of
DN160 can be put on a reel increasing
the efficiency of modern ploughing
technologies. With new ploughing
technologies and the need for longer
continuous lengths and larger diameters
in coil form, Low Ovality is well positioned
to remove the constraints of butt welding
backlogs and joint failures during the
installation and life time of the pipeline.
Reels of this size would require an escort
on highways, however, the cost savings
made through a much more efficient
installation process far outweigh the
additional transportation costs and with
fewer joints, maintenance costs of the
pipeline are also considerably reduced.
Even with pipe sizes that can
already be coiled with standard coiling
machinery, Low Ovality can make a
big difference to profit margins through
its ability to supply longer lengths of
coil within existing coil dimensions,
increasing the pipe length per truck and
so reducing overall transportation costs.
Transporting thinner walled pipes in coil
format also becomes a possibility with
Low Ovality as it is capable of coiling
pipes with SDR up to 21 and 26 while
maintaining coil and pipe stability.
Pipe Coil Technology Limited
– UK
Email:
chris.spratt@pipecoil.co.ukWebsite:
www.pipecoil.co.ukA low speed tube coiler for small diameter
tubing