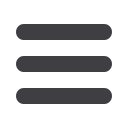

Coi l ing
and
uncoi l ing machinery
www.read-tpt.comJ
anuary
2013
91
PCT delivers world’s largest
traversing RTP coiler
PCT has recently delivered the world’s
largest traversing RTP coiler to a major
US pipe manufacturer. The coiler is
designed to enable efficient and cost
effective coiling of 50mm to 190mm
nominal bore RTP pipe. Free standing
coils weighing up to a record breaking
8.6 tonnes can be achieved in a safe
and controlled process which requires
minimal physical effort from a single
operator. The uniquely designed coiler
is rail mounted in order to traverse
the coiler as opposed to the pipe,
ensuring safe coiling without applying
strain from any off-axis bending of the
product. PCT is well established as the
market leader in large diameter coiling
equipment for plastic pipe and continues
to develop and expand its product
range. With the demand for ever longer
lengths of continuous pipe increasing,
PCT foresees a lot of interest in this
technology in 2013.
PCT’s Bryan Friend commented “Pipe
manufacturers are beginning to realise
that providing pipes in the traditional
‘stick’ lengths is no longer a viable
option. Installing pipelines using ‘stick’
lengths is incredibly inefficient due to
the unavoidable bottle neck of butt
welds or electro fusion joints every 12
or 20m. Installing long lengths of coiled
pipe takes a fraction of the labour force
and the number of welds is reduced
by a factor of 10-20 greatly increasing
the pipelines integrity whilst lowering
maintenance costs”.
With all PCT machinery, the new RTP
coiler comes with many automated
features as standard with optional
extras such as automatic strapping
and automatic integrated unload arm
available. PCT Ltd is a privately owned
company based in Newcastle, UK, with
subsidiaries in the USA and China. The
company designs and supplies coiling
and packaging solutions for flexible
products such as plastic pipe, sub-sea
umbilical and power cables, flow-lines
and steel wire rope.
PCT
– UK
Email:
coiling@pipecoil.co.ukWebsite:
www.pipecoil.co.ukCoil processing with decoiling
and recoiling lines
FORSTNER has developed and
manufactured machines for professional
processing of coils since 1960. From
the beginning, the prime objectives
of all development have been the
easy handling of coils and return of
the investments in Forstner lines. The
results are field-proven products made
with reliable designs ensuring extended
operating life.
A Forstner multiple decoiling, slitting
and cut-to-length line includes the
following units: up to eight powered
decoilers with bearing on one side
(cantilever); powered guidelines; eight-
fold coil selector for automatic selection
of any available material; programmable
or manual straightener with up to eight
rolls; programmable or manual slitter
with up to ten pairs of knives; electro-
mechanical guillotine; and SPS control
unit with touch screen.
Several decoilers are available, up to
a maximum coil weight of 12 tons. The
decoilers with bearing on one side can
be rapidly loaded with a crane, forklift
or a coil cart. The practicality of coil
selection, the valuable time saving and
the well-controlled decoiling procedure
ensure efficient fabrication. Powered
decoilers provide advantages for efficient
loading and ensure thorough protection
of valuable sheet. Even highly sensitive
types will be decoiled unscratched.
To meet the requirements of
fabricators of small and medium coils,
Forstner developed recoiling systems
that can be added to the slitting and cut-
to-length lines, as well as stand-alone
recoilers.
The company recently introduced the
new AUG 200 recoiler for small coils up
to 200kg. This cantilever recoiler has a
connecting terminal plug and works with
torque regulation. The recoiler handles
strips wider than 100mm and maximum
0.75 x 1,000mm, or 0.6 x 1,250mm mild
steel 400N/mm
2
.
Forstner Maschinenbau GmbH
–
Austria
Fax: +43 5522 74881
Email:
office@forstnercoil.atWebsite:
www.forstnercoil.atTube processing lines
IMEC Tubes develops and produces
tube processing lines, using more than
a decade’s experience to offer turnkey
solutions for tube finishing, handling and
bundling.
The company analyses customers’
production requirements and develops
custom-built layouts, offering new series
of patented machines to provide safe and
efficient solutions.
In addition to scarfing, rolling,
brushing,
end
facing,
storage,
bundling, coiling and quality control
(air-water and eddy current), one of
the company’s latest designs is the
patented permanent magnetic inside
bead system. The system does not
need a generator or tow-bars, and
activates and de-energises magnets
using an electric input.
IMEC
– Italy
Email:
sales@imec-tubes.comWebsite:
www.imec-tubes.com