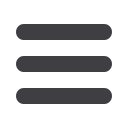

Inspection, measuring
and
testing
www.read-tpt.comJ
anuary
2013
87
Raising calibration standards
SCAN Systems is a company that offers
expertise in the areas of OCTG tubing,
casing and inspection. It has pioneered
numerous
revolutionary
products
designed to serve the OCTG tubing,
casing and NDT inspection industries.
One particular area in which it excels is
in creating artificial reference indicators
and precision flaws to create test
standards for NDT inspection equipment.
As inspection technologies have
advanced the need has become greater
for accuracy and precision in artificial
reference indicators (ARIs). As per API
specifications and the industries ever
growing demands, the equipment used
for testing must be calibrated against
known standards.
Often the very nature of the products
that NDT companies are dealing with
will cause great challenges in creating
ARIs, whether working with the need to
create a transverse flaw in between API
pipe threads to simulate a fracture, or a
requirement to manufacture a flaw 19ft
inside a pipe.
In many applications around the globe,
flaws are often created by hand, utilising
Dremel tools or grinding equipment.
These methods lack in precision for
width, depth, and geometry. In addition,
ID flaws in pipe are nearly impossible
without cutting the standard at the
location you intend to place the flaw.
The EDM process works well in
applications that require ARIs to be
created in larger parts. It is often used to
manufacture flaws in OCTG tubing and
casing. In certain configurations, an EDM
machine can offer portability giving the
operator the flexibility to create the test
standard in the field or production facility.
Great care and consideration needs
to be given when setting up the material
that will ultimately become the test
piece for phased array, UT or EMI
inspection to be done in the future. It is
these points in time that patience and
attention to detail can make or break
the entire NDT process.
That is why Scan Systems invented
the EDM NotchMaster product line
offered through its EDM Specialties
Division. The NotchMaster is the world’s
first portable EDM unit designed to
create precision flaws in both the ID and
OD surfaces of pipe or any other ferrous
material. The portable power supply
along with specially designed tooling
allows the NotchMaster, using the EDM
process, to slide inside the pipe, easily
creating a precision flaw at the precise
location required. Through this innovative
process, the EDM NotchMaster is able
to create longitudinal flaws, transverse
flaws, oblique angled flaws and wall
reductions of nearly any geometry.
The development and manufacturing
of the NotchMaster was a sign of Scan
Systems’ dedication to solving some of
the most important problems faced by
inspection companies in the field.
The EDM NotchMaster can create
precision flaws and control the depth
of the cut within two thousandths of an
inch. The width of the notch is controlled
by the electrode material chosen for
the application. Typically, the electrode
material is available from 0.006" to
0.040" wide. A flaw created by EDM will
create a width that is 0.005" wider than
the selected material.
The depth of the flaw is tightly
controlled, often through the use of
a digital micrometer. The micrometer
can control the depth of the notch to
two thousands of an inch. In addition,
in certain configurations, EDM can
be utilised to create flaws in the ID of
tubular products such as OCTG. Years
ago, a joint of tubing or casing would
have to be cut in half in order to create
a flaw in the ID of the pipe. With EDM
technology, the tooling has advanced to
allow an EDM notch to be created in the
ID of the pipe up to 96" up inside the
tube.
Once flaws are created, a replicate
of the flaw is one way to examine the
true measurement. A catalyst and base
material can be used to form a mould –
much like a dentist would form a mould
of your teeth. The mould that is created
can be used to verify an ARI that was
created inside a pipe.
Once the replicate is made, it will
be sectioned and put under an optical
comparator to measure the exact depth
of the flaw. The replicate material can
also be used to help examine the angle
and surface of a flat bottom hole. These
replicates of theARIs created for that test
piece can be filed with the certification
paperwork for any audits that may occur
in the future.
The Notchmaster is applicable not
only to OCTG tubular products, but
to other industries as well, such as
the line pipe industry, forging industry,
aerospace and automotive products.
The tool has been the best of its kind
on the market for two decades and will
prove itself valuable to any company
in an industry that requires calibration
standards.
Scan Systems
– USA
Email:
mattr@scansystems.comWebsite:
www.scansystems.com