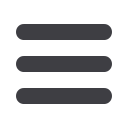

53
www.read-wca.comWire & Cable ASIA – January/February 2015
From the Americas
Steel Industries since 1984. According to Toshiyuki “Ted”
Tamai, its current president and CEO, a firm decision was
taken early on that there would be no recession-related
layoffs, furloughs, or base-salary cuts. (“California Steel
Industries Weathered Recession with No-Layoff Policy,”
10
th
October)
How was this accomplished? Among the cost-cutting
measures reported by Ms Gruszecki:
Reassigning 30 employees to a furnace construction
project.
Taking in-house some services that had been contracted
out.
For nine months, suspending the corporate matching
contribution to employee retirement plans.
Permitting voluntary reduction in employee work hours.
Most notably, paying 100-plus employees for more
than $250,000 worth of community service work.
Projects included cleaning up the San Bernardino
National Forest, refurbishing a battered women’s shelter,
rebuilding a burned-out ranch, and landscaping the
grounds of a college.
Even as orders tumbled, one employee was paid an
hourly wage for a five-week stint with the US Forest
Service. “It saved my house,” he told the
Press
Enterprise
. “It was a real morale booster.”
Mr Tamai noted that, during his company’s
full-employment retrenchment, other steel companies
across North America laid off 16,300 workers. In 2009
alone, he recalled, there were 7,765 jobs cut at US Steel.
California Steel is the only West Coast steel company
that makes hot rolled, pickled and oiled, galvanised,
cold rolled sheet. The largest industrial employer in the
inland area of the state, it has seen its workforce grow
by 120 since the downturn to 1,077 today.
Aluminium
In a brightening climate for aluminium,
Alcoa ‘bets big’ on aerospace with the
world’s largest aluminium-lithium plant
Aircraft manufacturers are increasingly turning to lighter
and stronger aluminium-lithium alloys, which are less
expensive than titanium and composites and afford better
fuel efficiency and lower maintenance costs. To capture that
demand, Alcoa on 2
nd
October opened an aluminium-lithium
plant in Lafayette, Indiana, where it produces advanced
third-generation aluminium-lithium alloys for the aerospace
industry.
The $90 million facility is the largest of three such projects
for the company. New York-based Alcoa has also expanded
its aluminium-lithium capabilities in Pittsburgh and at the
Kitts Green facility in the United Kingdom.
The cast house at Lafayette has a rated capacity of more
than 20,000 metric tons annually, making it the largest
aluminium-lithium facility in the world.
The product line includes extruded, forged and rolled
parts for aerospace applications: single-piece wing skins,
fuselage skins, wing stringers, floor beams, seat tracks and
other components. The company also has in development
an aluminium-lithium forging for the front fan blade in
Pratt & Whitney’s PurePower engines.
Shortly before publication of Alcoa’s third-quarter 2014
results,
Forbes
noted that the company has “bet big”
on the aerospace segment in its strategic shift towards
value-added products. Signs are strong that the big bet
will pay off. (“Value-added Businesses to Boost Alcoa’s
Q3 Results,” 2
nd
October)
Certainly the current outlook for aluminium is favourable
to Alcoa’s business in general. Cuts in global smelting
capacity in response to low prices have finally taken effect.
Forbes
reported that London Metal Exchange warehouse
stocks of aluminium were down around ten per cent in
mid-2014 from the start of the year. A poll conducted by
Reuters in July found that the market for aluminium is
expected to move from an oversupply of 235,500 tons last
year to a deficit of 4,444 tons in 2015.
While that deficit will likely see some erosion from smelting
capacity restarts, the tightening of the physical supply of
aluminium has led to a recent rally in prices. LME aluminium
prices averaged close to $2,000 per ton in the third quarter
of last year. They averaged roughly $1,800 per ton over the
course of the third quarter of 2013.
Automotive
An American steel-industry trade
organisation predicts that aluminium use
in cars will go into reverse around 2018
Alcoa may be setting its sights on aerospace (see
“Brightening climate for aluminium,” above). But, as
US carmakers work to meet stricter global emissions
standards and to comply with Corporate Average Fuel
Economy (CAFE) goals, automotive is the arena of the
steel-aluminium faceoff. The domestic steel and aluminium
industries both expect aluminium use in cars to grow.
A study commissioned by the Aluminium Transportation
Trade Group predicts that seven out of ten pick-up trucks
will have aluminium bodies by 2025.
While steelmakers acknowledge that the automotive
industry is using more aluminium all the time, a report from
the steel-industry trade organisation World Steel Dynamics
Inc (Englewood Cliffs, New Jersey) claims that the trend
will be short-lived. Over 300 pages it argues that the weight
advantage of aluminium will be neutralised by the arrival of
more advanced, lower-cost and lighter-weight steels.
Reviewed by Stephen Edelstein in
GreenCarReports
,
“AutoBody Warfare: Aluminum Attack” foresees aluminium
use peaking around 2018, even as CAFE standards stipulate
additional fuel-economy gains. (The mandated fleet average
– the equivalent of around 42 miles per gallon on the
window sticker – is 54.5 mpg by 2025.)