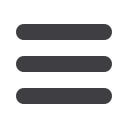

PETROCHEMICALS
Chemical Technology • February 2016
5
mendations which support the customer in making deci-
sions and defining actions to optimise the maintenance
strategies for the respective installed base; and
• Endress+Hauser management of the customer’s day-
today maintenance processes and activities with specific
focus on field instrumentation. This service is facilitated
by a partnership agreement.
Endress+Hauser (in consultation with the process owner)
identifies, defines and then reports on areas of mainte-
nance focus and potential improvements by means of Key
Performance Indicators (KPIs).
This KPI framework positions the partnership to act
effectively in addressing the respective maintenance
requirements and improvement areas on-site. By com-
bining your process competence with Endress+Hauser’s
automation know-how, we are able to collaborate as a
team. Through a planned and practical approach we can
improve your maintenance efficiency, while achieving
or maintaining compliance with your safety, quality and
environmental requirements. Our experts can propose im-
provement actions that are aimed at decreasing process
interruptions and minimising your maintenance efforts
and associated costs.
Benefits
• Decreasing the complexity of your installed base through
standardisation. This allows for improved personnel ef-
ficiencies and optimising/minimising spare part stock
holding;
• Achieve safety and quality compliance by optimising your
maintenance efforts within an effective maintenance
schedule;
• Minimise downtime by ensuring and preparing for ef-
fective responses to the break-down of critical assets
within your process;
• Complete visibility and traceability of your installed base
of assets. This extends to updated information and
documentation availability throughout your installed
base’s life cycle.
Deliverables
• A comprehensive Installed Base Status Report listing
recommended areas of improvement needed to achieve
a balanced maintenance plan.
These areas include:
□ Standardisation within the installed base
□ Reactive maintenance preparedness
□ Preventative maintenance strategy
□ Migration relevance within the installed base based upon
dynamic product statuses of the respective assets
• Quick and easy online access to all information related
to Assets in the installed base using Endress+Hauser’s
Web Enabled Asset Management Platform (W@M)
Proximity… No matter where you are in southern Africa or
whatever the industry, we are always ‘By Your Side. Service
is an integral part of our offer’.
Our Service Team is strategically located across the
country ensuring active local presence to meet all your
service needs. For those really isolated sites, such as mines
and offshore platforms, our remote services offer provides
maximum support for your maintenance teams.
For more information contact
Glenn Smith, Added Value Services Development Manager,
Endress+Hauser (Pty) Ltd, on tel: +27 11 262 8000;
or go to
http://bit.ly/1TbZvzYCOVER STORY