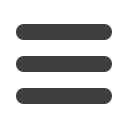

ÖLFLEX
®
ACCESSORIES
FLEXIMARK
®
SILVYN
®
SKINTOP
®
EPIC
®
HITRONIC
®
ETHERLINE
®
UNITRONIC
®
APPENDIX
For current information see:
www.lappgroup.com1198
Appendix
Glossary
Core
The optical core in glass fibre cable technology.
Core check, response at increased temperature
In order to determine the influence of heat on the mechanical properties
of, for example, insulating covers, a test item is placed in a device for
heat pressure testing which has already reached the testing tempera-
ture. The wall thickness of the test item determines the test load. After
a specific storage period in the heating cabinet and subsequent cooling,
the impression depth is measured with the reading microscope.
Core check, response with thermal shock
The core insulating cover is checked for thermal shock by wrapping the
cores or strips from the insulating cover around a defined mandrel and
storing them in a heating cabinet for approx. 1 hour at 150 °C. After
removing the cores/strips and cooling them to room temperature,
these test items should not display any visible cracks.
Core diameter
The core diameter is the diameter of the central light-carrying section
of a light waveguide.
Core group
For the transmission of signals or energy, two or more stranded cores
are required. Using two cores, it is possible to form a circuit that can
transmit energy or signals.
Core Ident Code
VDE-DIN-colour code for colour-coded low-voltage cables according
to VDE 0293-308/HD 308 S2.
Core identification
Coloured or numbered identification of single cores. A Lapp develop-
ment: The internationally proven ÖLFLEX
®
colour code is based on the
colour-coded identification of the single cores. Ten basic colours are
combined with 2 mm wide colour spirals. This results in 102 colour
variations. This colour marking is particularly advantageous compared
to cores printed with numbers, as it means the cores can be assigned
much more quickly in a device (saving time).
Core joint
Core joints combine synthetically insulated signal cable and telecom-
munication cores in a conductor diameter range of 0.35 – 0.9 mm. The
cores are pressed together using a special core-joining pliers and thus
placed solderless into the connection sleeve.
Core print
In the manufacture of cables, cores are principally identified by four
methods:
1. Cores can be manufactured in one primary colour.
2. Marked with various colour codes.
3. Printed.
4. A combination of the different colour codes with printing. It must be
noted that only earth conductors are to be green-yellow in colour
and that these colours may not be used if there is any risk of confu-
sion with other cables.
Core stranding
Without stranding, wires positioned parallel to one another would
deform when bent. The outer wires would be overstretched and the
inner wires compressed. The individual wires are twisted together in
a spiral to maintain the flexibility and mobility of the conductor. The
result is known as core stranding.
Core stranding with more than four cores
When constructing a cable, the best layer structure of the stranding
elements is always selected, to obtain cables that are as circular as
possible. Gaps in the layer structure are filled with insulated fillers or
central cores (filling elements). In flat cables, the structural elements
(groups or cores) are parallel to one another and can be stranded.
Core wrapping
Core wrappings are used to protect the insulating covers of rubber-
insulated cables. They are mainly made from foil or fabric tape.
Core, conductor, insulated wire
Individually insulated conductor, e. g. made of single- or multi-wire
copper or aluminium. Core = conductive component of cables with insu-
lation coloured or marked numerically.
Corrosion
Degradation of minerals and materials due to mechanical and chemical
environmental influences.
Coupler
Passive optical components for transmission of light between a light
source and a light waveguide or between several light waveguides.
Couplers that allow light waveguide networks for connecting multiple
transmitters and receivers to be set up are of particular importance
(see → T coupler).
Crane cables
Crane cables are supply cables for cranes in the open air or indoors
(e. g. ÖLFLEX
®
CRANE at Lapp).
Crimp connection
Mechanical joining technology. When joining, for example, coaxial
connectors with a coaxial cable using a crimping tool, a metal sleeve
is pulled over the shielding and pressed together.
Cross-linked
The term refers to a manufacturing process for elastomers, thermo-
plastics and duroplastics. It describes the fact that particular chemi-
cals are used to change the original linear alignment of the macromol-
ecules from planar to solid structures. The materials used include
sulphur compounds for rubber and peroxides for thermoplastics and
duroplastics. Cross linking is carried out under the influence of heat
and pressure, and high energy rays for thermoplastics. Cross linking is
a permanent and irreversible process and plays a critical role in deter-
mining the actual material properties (it gives rubber its permanent
elasticity and improves the thermal, mechanical and electrical proper-
ties of polyethylene).
Cross-linked polyethylene XLPE
Cross-linked polyethylene.
Cross-linking agent
Cross-linking agents or vulcanising materials in rubber compounds are
either sulphur (for natural or synthetic rubber) or peroxide (for silicone,
EPDM). Sulphur cross linking begins at room temperature and intensi-
fies as the temperature is increased. With peroxide cross linking, oxy-
gen is released for cross linking at a specific temperature.
Cross-section
Cross-sectional area of the conductor. A distinction is made between
the geometrically defined nominal cross-section and the conductive
cross-section, which is derived from the electrical → resistance.