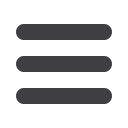

Stainless steel production
www.read-tpt.comM
arch
2013
75
Bending, measuring and further
bending stainless steel in one go
THOSE who want to accurately bend
steel or stainless steel tubes and tube
systems must accept long auxiliary
processing times for the generally
unavoidable measuring and adjusting
process. This is because the rebound
behaviour of the materials can differ
widely – even if the tubes come from
a single batch. The production of
prototypes and individual items is
similarly time and labour-intensive. The
Springmatic optical measuring system
provides a remedy here: the new
development from Schwarze-Robitec,
which is integrated into the bending tool,
measures the bent tubes directly while
tensioned on the bending machine
and immediately starts the required
further bending process if desired or
saves the required correction value for
subsequent bends.
Instead of removing the tube after
the bending process, checking it on
an external measuring system then
retensioning it for subsequent bending,
tube processing companies can
bend, measure and adjust in a single
stage with the aid of Springmatic.
Immediately after the bending of a tube,
the new optical measuring system that
Schwarze-Robitec is integrating into
its bending tools records the rebound
value, from which the CNC control of
the tube bending machine calculates
the required subsequent bending angle.
Subsequent bending is carried out
immediately afterwards – either fully
automatically if desired or after clearance
by the machine operator. “This integrated
form of dimensional stability check and
tube post-processing takes only a few
seconds per work piece on average.
This is contrasted with around three
to five minutes required for measuring
and adjusting in the conventional way,”
Schwarze-Robitec plant manager Jürgen
Korte reports.
When developing the measuring
system, the tube bending specialists
from Cologne placed particular
emphasis on a very broad range of
applications:
Springmatic
reliably
checks both thick and thin-walled tubes
in the broadest range of materials
and diameters. The system can be
integrated into almost any bending
tool and combined with almost all tube
bending machines from Schwarze-
Robitec. “The measuring accuracy from
Springmatic is naturally equivalent to
the accuracy of conventional external
systems,” Schwarze-Robitec managing
director Bert Zorn added. “Furthermore,
users not only save up to nine tenths of
the auxiliary processing times previously
required; in individual item and prototype
production, they additionally benefit from
a noticeable material saving as almost
every component is now also a useable
bulk component. These advantages
have an effect particularly in tube
production for the automotive, machine
and plant engineering and shipbuilding
industries.”
Schwarze-Robitec GmbH
– Germany
Email:
sales@schwarze-robitec.comWebsite:
www.schwarze-robitec.comOptimising steel production
capacities around the world
THE products of Sinico Machine Tool
Manufacturing, Italy, have a wide field
of application and versatility, and have
been instrumental in rapidly expanding
Sinico’s market in many countries
around the world.
As a result, the company has
secured over 1,500 orders, delivered
to companies working in a range of
different sectors, such as firms in the
business of producing components for
cars, bicycles, motorbikes, electrical
motors,
household
appliances,
power transmissions, hydraulics,
pneumatics, pipe fittings, earth moving
machinery, chains, tools, rods, nuts
and bolts, bearings, dies, doors and
windows, and furniture, in addition to
contractors.
In Sinico’s offices and workshop,
single- or double-bar machines are
designed, developed and produced,
down to the very last mechanical
component, for standard applications
or tailored to the customer’s specific
needs.
Sinico is specialised in the design
and manufacture of automatic rotary
transfer cut-off and end-finishing
machines, suitable for producing
medium and large series of metal parts
from tubes, bars, coils, forgings and
blanks.
End-finishing operations commonly
performed with chip-removing machine
tools include facing, chamfering,
centring, turning, drilling, threading,
tapping, milling, grooving and splining,
as well as shaping operations such
as flaring, tapering, rolling, pressing,
marking and knurling.
Sinico machines can handle all
metal materials (steel, stainless steel,
aluminium, copper, brass, titanium,
Inconel, etc), and all operations are
carried out in one chucking. Various
different units of measurement, part
shape and cleaning control options are
also available.
The main features of the latest
generation of Sinico machines are:
ease of use; performance; quick
setup and automatic positioning of
units; optimised cutting process;
connection with LAN and WAN; self-
diagnostics with built-in graphics; user
info, maintenance data and functional
diagrams viewable on PC; and the
option of installing SPC (Statistical
Process Control) and messenger
(email/SMS) systems in case of
machine alarm, as well as remote
servicing with web cam.
Sinico Machine Tool Manufacturing
Srl
– Italy
Fax: +39 0444 644857
Email:
info@sinico.comWebsite:
www.sinico.com