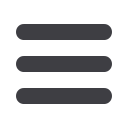

M
arch
2011
43
›
T
echnology
U
pdate
Quick-change mill with roll adjustment
T&H LEMONT has shipped a complete
Model WU20H-11 high frequency quick
change, high frequency welded mill in
North America.
The tube size range of the WU20H
mill is from 0.5" to 2.5" OD round tube,
with wall thickness ranging from 0.03" to
0.16". Along with round tubing, the mill is
designed and tooled to produce the related
shapes. The mill will produce tubing at
speeds up to 600fpm.
To facilitate production at this speed,
a T&H Lemont horizontal accumulator
was included with the entry system. The
horizontal accumulator will have sufficient
storage to assure all end welds can
be completed without interrupting mill
production. The rugged turntable design
will provide long service with a minimum
of maintenance.
To increase productivity and improve
the quality of the tube, the mill is equipped
with a number of state-of-the-art features.
To minimise roll adjustment time, the
mill features the AutoSet automatic roll
adjustment system, which utilises patented
absolute encoder technology to achieve
highly accurate, repeatable setups.
A colour touchscreen interface is used
to select mill setup from a menu of product
specifications, based on previously stored
setups. The operator will enter an ID specific
to the pipe or tube size, and the screen
will show nominal rim gaps in addition to
actual rim gaps as entered from previous
production of that size tubing. The stands
automatically adjust to those locations at
the touch of the screen, and each stand is
represented on the touch screen.
The operator can make minor adjustments
from the touch screen in 0.001" increments.
Once the best setup is achieved, the data can
be stored as the new product specification.
The system is capable of storing 100+ unique
mill setups.
The absolute encoders retain position
information with ‘power off’ and never require
a ‘zero-out’ procedure. For example, if an
adjustment is made manually while the
system is shut down, at ‘power on’ the
system will recognise the new position. In
place of expensive servo motor drives, the
system features standard AC vector drives
to replace manual adjustment of the driven
stands. The AutoSet system includes as
standard an Ethernet interface and web
server for data acquisition.
The mill includes a complete second set
of rafts for the quick-change of tooling from
one size to the next. This second set of rafts
incorporates the T&H Lemont AutoSet roll
adjustment system.
In addition to the AutoSet automatic roll
adjustment system, the mill also features the
T&H Lemont Pro Display productivity display
system. This system provides information,
presenting key metrics such as mill speed,
production levels, downtime and uptime on
a large flat screen monitor. Target production
rates versus actual production rates are
continuously displayed. All data is logged to
memory and exported to a central computer
for analysis. In addition, the system will
display the information on any plant PC, text
message downtime alerts to supervisors and
management, and email shift performance.
To complement its line of complete
production systems, T&H Lemont provides
a variety of components and services to the
tube and pipe industries. Services include
tube and pipe roll design, mill alignment and
operational consulting. Components offered
byT&HLemont includewelders, cut-offs, entry
equipment, accumulators, seam orientation
stands, weld boxes, edge conditioner, bead
scarfing systems, straightening systems,
single point adjustment systems, dedimplers,
rolls, blades, jaws and shafts.
T&H Lemont
– USA
Fax: +1 708 482 1801
Email:
sales@thlemont.comWebsite:
www.thlemont.comWU20H forming section