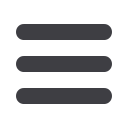

M
arch
2011
45
›
T
echnology
U
pdate
IT’S THE TOOLS
THAT SAY HOW GOOD YOU ARE
www.t-drill.fi,
sales@t-drill.fiHighly automated tube branching for
automotive and air conditioning industries
Industry standard collaring station
with integrated pilot hole milling,
collaring and trimming
Stainless steel
strip accumulator
from Italy
WITH the growing popularity of plants that produce stainless
steel tubes using a laser welding system, which has helped
to increase processing speed, there is now a need to create
an accumulation system with sufficient capacity for joining
the head/tail of the strip and thus to replace obsolete cavity-
type or looping accumulation systems. That’s the reason why
Oto Mills created the FBS INOX accumulator, which was
developed with the company’s thirty years of experience with
this type of unit.
Besides offering the proven advantages of Oto Mills
accumulators, FBS models have a series of additional
custom features that were exclusively developed for use with
stainless steel. In particular, all the rollers and surfaces that
contact the strip have been specially treated so that they
maintain the surface of the material intact.
Also, a special control system is used that optimises
accumulation to prevent the strip from being scratched and
ruined, while still maintaining the capacity that is required for
joining the coil in a way that is suitable for being fed into any
production line placed after the accumulator – even those
that are obsolete and which require a great deal of time for
preparation and for joining the strip.
The FBS Inox accumulator is essentially composed of two
groups of rollers that form the inner drum and the outer drum,
which are arranged in two concentric circles.
The inner drum is fixed, while the loading drum rotates
around its axis.
The strip is unwound by the decoiler and loaded by a
pinch-roll into the machine at a speed that is higher than the
line to be fed. The strip is drawn in by the loading roller as the
loading drum rotates. Besides drawing the strip, the loading
roller also transfers it from the loading drum to the inner drum
when the machine is loaded or emptied.
As the strip is extracted by the tube formation line,
it moves from the inner drum, turns around a centrally
mounted roll set, and is pulled over the asymmetrical gap
between the entrance and the exit by the entrance and exit
rollers and the slanted rollers.
During machine operation, the strip is removed from the two
(internal and external) coils of accumulated strip with virtually no
friction. As a result, the force required for extracting the material
from the accumulator is relatively small.
The strip is restrained at the sides by lateral guide
rollers which rotate on bearings. Strips of any width and
thickness (within the operating range of the machine) can be
accumulated. However, the thickness and width of the strip
must be adequately proportioned, since the accumulation
properties of a strip that is thin and also small in size largely
depend on the type of material the strip is made of.
Oto Mills
– Italy
Fax: +39 0522 964188
Email:
otoinfo@otomills.comWebsite:
www.otomills.com