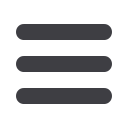

T
echnology
U
pdate
›
www.read-tpt.comM
arch
2011
49
www.boilertubes.de1/4-Seite (60 x 180 mm) Satzspiegel
(Tube & Pipe Technology + TubeProducts Int.)
Pipes . Tubes . Services
Handling
of delicate
pipes
THE handling of long and thin stainless
steel pipe is extremely difficult. This is the
main reason why there are few companies
who can supply a pipe transport system
that ensures high process capability with no
damage to the pipes.
Among these companies is Reika GmbH
& Co KG, whose experience in the sector
of finishing lines was demonstrated with the
construction of a fully automated finishing
line with integrated non-destructive testing
line for Scandinavia’s largest manufacturer
of stainless steel pipes. The customer’s
intention is to use this line for the transport
of high-grade stainless steel duplex pipes
for heat exchangers with diameter of up
to 25mm and length of up to 30m. These
pipes need to be handled with utmost care,
not only due to their dimensions but also
because they are polished.
All automatic finishing lines made by
Reika are highly specialised systems for a
production that requires very little personnel.
The special transport systems are used for
longitudinal as well as cross transport,
including numerous applications such as
straightening, machining, pipe marking and
various testing applications. Sophisticated
material tracking systems ensure process
capability and material identification.
This line has been designed by Reika
to meet the specific requirements of the
customer, for example by integrating special
solutions in the areas of pipe return and batch
assignment. The manufacturing of the entire
line was carried out in only six months.
Reika’s product range is comprehensive,
especially in the sector of finishing lines. It
includes finishing lines for hot rolled, cold
pilgered and longitudinally welded tubes,
hot rolled bars and precision bright bars.
Depending on the customer’s requirements
the production steps of straightening,
testing, parting, chamfering and bundling
are integrated into the finishing lines. This
also includes comprehensive services such
as output maximisation due to optimising
strategiesorcustomisedconcepts.According
to Reika’s experience the optimisation of the
individual pipe lengths by automatic flaw
cutting and consideration of samples, tube
ends and final lengths reduces the scrap
by 2 to 3%.
Reika finishing lines are available for
diameters between 10 and 610mm and wall
thicknesses of 1 to 50mm. Bar finishing lines
are manufactured for diameters between 10
and 180mm.
Reika GmbH & Co KG
– Germany
Fax: +49 2331 9690 36
Email:
sabine.gerstkamp@reika.deWebsite:
www.reika.deINSPECTECH Analygas Group has
provided customised NDT solutions for the
tube and pipe industries for over 30 years.
The company was recently challenged by a
customer’s requirement to nearly double the
production rate on its off-line ultrasonic test
system for API product.
InspecTech modified their existing off-
line ultrasonic weld line inspection system
by adding a second mechanised test head
to the existing gantry. An upgraded master
control panel was designed and built as
well, with improved logic to manipulate the
dual test heads.
The upgraded test cell meets the
customer’s needs for additional test capacity
at a fraction of the cost of a second complete
test unit. With a dual test head inspection,
one test head inspects two thirds of the tube
length, while the second test head tests the
remaining third, including the starting end of
the tube. The InspecTech off-line ultrasonic
weld line test system does not leave untested
ends, providing 100% inspection.
InspecTech has provided flaw detection
systems using eddy current, flux leakage
and ultrasonic technologies in both on-line
and off-line applications for international
markets.
InspecTech Analygas Group
– Canada
Fax: +1 416 757 8096
Email:
sales@inspectech.caWebsite:
www.inspectech.caTwo heads are better than one
Medical
services
MANCHESTER Tool & Die, Inc offers
prototype, short or long run machining for
medical components.
Housed in a 50,000ft
2
manufacturing
facility, wire EDM, CNC milling centres
and star turning centres are available for
medical part production, along with various
surface finishing and washing machines.
Manchester Tool & Die also provides
in-house engineering, a complete tool room
and on-time delivery.
Manchester Tool & Die Inc
– USA
Fax: +1 260 982 4575
Website:
www.manchestertoolanddie.com