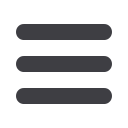

106
Wire & Cable ASIA –September/October 2016
www.read-wca.com❍
❍
Figure 4
: Planetary back-twist
❍
❍
Figure 5
: Induction motor power and torque curves
Torque (Nm)
Speed (rpm)
Power (kW)
Speed (rpm)
❍
❍
Figure 6
: Speed and torque on each back-twist shaft
❍
❍
Figure 7
: Torque curve on a gear
Back twister 1 – wheel 2 –
torque mag (Nm)
Time (s)
In other words, this activity is the scientific and precise
application of the design of experiment (DOE).
Rigid body dynamics model
A rigid body dynamic analysis is performed; internal loads
and motor power torques mainly depend on accele-
ration and inertias of moving parts, so that there is not a
clear need of introducing flexibilities into the model (which
would significantly increase the computational effort).
Starting from the MFL 3D CAD geometry of the machine,
the dynamic model is defined in the RecurDyn
®
environment.The result is an accurate model with more
than 100 bodies.
Most of the inertial proprieties are derived automatically
from CAD, but several bodies are parametrised inside the
multi-body software.
Obviously, the connection between the different bodies
perfectly simulates the real kinematic link (gear, shafts,
and so on) in order to obtain a model which is the closest
as possible to the real machine in terms of degrees of
freedom.
Gear elements are special features of the RecurDyn
®
library, designed to simulate both kinematics (transmission
ratio) and dynamics (reciprocal loading) occurring at any
gear couple.
Figure 4
shows the gears back-twist system. It is
easy to see that the “gear feature” of RecurDyn
®
has
been massively used due to the conformation of the
transmission chain.
When each simulation runs, all loads are automatically
combined together along the transmission chains, leading
to a precise estimation of the power demand at all motor
shafts.
As active parts of the machine, the electric motors, are
modelled taking into account the real inertia of the rotating
parts and using the real constructive curves (torque and
speed) of modern induction motors.