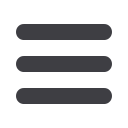

107
www.read-wca.comWire & Cable ASIA – September/October 2016
❍
❍
Figure 9
: Cradle equivalent deformation and Von Mises stress
Deformation
Vertical position
Vertical position
Von Mises
stress
Deformation
Horizontal position
Von Mises
stress
Horizontal position
Otherwise by using ideal motors (very easy and simple in
RecurDyn
®
) there would be the risk to obtain an imprecise
answer. In fact, such an approach would generate
unrealistic torque peaks in the simulated signals; motors
with unlimited torque simply do not exist.
Figure 5
shows an example of motor laws.
Dynamic simulation and results
A lot of dynamic simulations are run, and more than 60
cases are analysed, based on the possible different load
cases preliminarily defined.
Each dynamic simulation is composed of three phases:
acceleration (from zero to the maximum speed), a steady
state condition at the maximum speed, and the emergency
braking (deceleration from maximum speed to zero in a
few seconds).
From the large volume of data collected it is possible to
define all the information necessary for the design; in
particular the maximum power required to the motors and
the maximum torque and speed on each part.
This data is fundamental for the right choice of motors and
for a good structural design of the parts (rotor, cradles,
joints, and so on).
Figure 6
shows the results in terms of rotation speed and
torque on each part of the transmission chain.
Figure 7
shows a typical torque output on a gear. The peaks, clearly
visible in the curve, are due to spools unbalance.
Dynamic results as structural input
As previously explained, the results obtained from
the dynamic simulation are the input of the structural
simulation.
❍
❍
Figure 8
: Load on cradles
Horizontal Force
Vertical Force