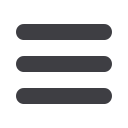

Eternal India
encyclopedia
ARCHAEOLOGY
The
Atiratra
ceremonial commencement of the
sattra
is mentioned
in the
Rig Veda
(VII. 103.7). The Harappan seal depicting an offer-
ing being made by a devotee to the Fire God standing in the midst
of pipal (
Asvattha)
branches, and witnessed by 7
r is his
in a row
below may refer to the seven star group of
Krittikas
(Pleiades).
Agni
(or
Arka
of the Harappan seals) being the deity of the
Krittikas
in the
Vedic
hymns the same group of 7 stars
(rksa)
in the
seal under reference may indicate commencement of the sacrifice
(as indicated by a sacrificial animal behind the devotee) in
Krittika
Naksatra.
The term
Magha
occurs in Indus inscriptions also (Rao
1990,284 ff). The performance of the
gavam ayana sattra
in Lothal
and Kalibangan seems to indicate keeping count of days, seasons,
and year so that the calendar could be accurate. This was the
purpose of the Vedic sacrifices also. W.J. Fairservis (Jr.) has sug-
gested the use of two graduated rods of shells from Mohenjo-Daro
as calculators of days, months etc. (Fairservis. W.J (Jr.)
1977.71,122). Gurov’s view (
Science Today
, Bombay, March
1982) that the Pleiades was
v
a 6 group star in Harappan times as
suggested by a seal with 6 vertical lines and a fish sign (for star)
does not stand to reason because even in the Vedic period it was a
7-star group and must have been so in the Harappan times. Hence
neither the fish sign stands for star, nor the cardinal number 6 for
Pleiades.
Chemical practices
Beginnings of chemistry can be seen in the ceramic art of
Mehrgarh in the 5th millennium B.C. Baking clay involved pro-
longed heating, fusion, and control of temperature in the kiln.
Chemical processes involved in etching on carnelian beads by
drawing the pattern with a solution of alkali, generally soda, was
well-known to the Harappans at Lothal and Chanhu-Daro. A
black-on-white design was produced by flooding the stone with the
alkali and drawing a black pattern on top of it with a solution of
copper nitrate. Near the bead factory at Lothal a kiln was also built.
The steatite seals were coated with an alkali and heated to produce
a white lustrous surface. The most amazing production of the Har-
appan lapidaries is the microbead of steatite, smaller than a pin-
head in size uniformly bored and cut. In one gram sample 310 beads
were found. The quantitative chemical analysis shows 60% silica,
30% magnesia, 6% alumina, less than 2% lime and less than 1%
iron. Such calcose occurs naturally with metamorphosed ultra basic
rocks. There are still differences of opinion among scientists as to
how such microbeads of the hardness of 6 to 7 on Moh Scale could
be produced. Perhaps the steatite paste rolled on a string was put
in fire. After baking the tubular roll it was cut into small pieces.
Prof. K.T.M. Hegde however suggests that the paste was pressed
through a squeezer.
Geology, Mining and Metallurgy
A sound knowledge of Geology on the part of the bead-makers
of the Indus Civilization can be assumed as they used extensively
chert, carnelian, chalcedony, crystal, jasper, agate, opal and many
other varieties of semigems. They knew the property of stones and
subjected them to heat, chipping and grinding. They possessed
good knowledge of metals, their sources, the technique of smelting
the ore and purifying and alloying metals. The occurrence of a large
variety of arrowheads, chisels etc., of copper near Ganeswar in
Rajasthan suggests, according to R.C. Agrawal, the working of the
Khetri copper even in pre-Harappan times. The Mohenjo-Daro
smiths used copper oxide ore. Two mud-lined pits of wedge-
shaped bricks in DK Area served as furnaces. Bronze-making and
metallurgy had reached a high degree of technical excellence at
Lothal. The copper ingot at Lothal is known for 98.81% purity
without any arsenic content while the copper ingots of Mohenjo-
Daro contain arsenic. The Khetri ore has also arsenic. Obviously
the Lothal smiths must have further purified copper and used it for
making a large number and variety of tools, ornaments and weap-
ons, which do not contain arsenic. The reference to
Guburum,
in the
famous Ur tablets addressed to the Dilmun merchant selling copper
ingots seems to be to the pure copper of Lothal which had extensive
trade relations with Bahrain and the Mesopotamian cities of Ur,
Kish, Brak and Arpachia (Rao 1973-80, 114-115 Bibby 1972, 235).
The Enki and Ninhursag myth contained in a large tablet from Ur
and translated by S.N. Kramer ‘Dilmun is holy and pure ‘ (Kramer
1963). It is a land where the sun rises first, the cities are clean and
the elephants live. This reference could be to the Indus Valley and
Lothal and not to Bahrain, although G. Bibby and others claim
Bahrain to be Dilmun (Bibby 1972, 376-7).
Some archaeologists' view that the Harappans did not know
how to make bronze is not correct because both copper and bronze
objects are found in Indus cities. The alloy was made with tin in
most cases but arsenic was also used for hardening copper. The
quantity of tin used in bronze varied from 5% to 13%. The Harap-
pans did not produce sophisticated weapons such as the sword,
dagger and spear having midrib, primarily because they feared no
invasion and utilized their knowledge
for producing tools needed by the
shipwright, carpenter and smiths. The
twisted drill and circular saw of
bronze from Lothal are excellent ex-
amples of sophisticated technology
used for peaceful purpose. The Har-
appan smiths knew
cire perdue
tech-
niques for casting as exemplified by
the figure of dancing girl of Mohenjo-
Daro (fig:34). They used more than
one mould for casting figures of birds
etc, and passed on this advanced
technology to the Late Harappans at
Daimabad where beautiful bronzes of chariot (fig:35), elephant,
rhinoceros and buffalo have been found. These figures contain tin
in varying proportions of 9.85% to 4.58%. As they are made of low
bronze the melting point of the alloy was between 1083
Q
C and