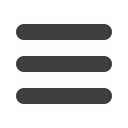

87
CHAPTER 4
PROCUREMENT AS A SUPPORT AND STRATEGIC FUNCTION WITHIN COMPANIES
The operations and technical representatives are co-located with the marketing
groups. The procurement director converses weekly with the operations and
technical people, who report to the same vice-president. These discussions
provide early insight into new products that might affect the development of
strategic sourcing plans.
4.7.1.3 Case Study: Putting the Pieces Together at Air Products
Air Products, a successful industrial gas producer headquartered in the eastern
US, operates air separation facilities worldwide. Over the past 15 years, industrial
buyers have increasingly viewed industrial gases as commodity items, which,
along with intense global competition, have created extensive downward
price pressures. It is only recently that industrial gas prices, like most other
commodities, have firmed up worldwide. The need to manage costs, however,
is a continuous requirement.
Air Products has operated historically as an engineer-to-order company, which
resulted in a great deal of engineering and design work customised for each
new air separation project. New production facilities designed and constructed
by the company have largely been engineered without considering previous
designs or leveraging commonality across design and procurement centres in
the eastern US and the UK. Historically, even if the US and Europe required a
similar or same item (which was often the case) or designed the same facility
in terms of its physical process and technology, each would have components
and equipment developed separately by engineers and procurement staff
that did not co-ordinate their efforts. As a result, design specifications differed
unnecessarily across regions. Duplicate engineering and sourcing drives up
costs with no corresponding benefits. From a technical perspective air separation
is technically a comparable process around the world.
Executive management concluded that the company must pursue standard
design and off-the-shelf product-based thinking on a worldwide basis. The
company’s objective was now to enter the global marketplace as a single
integrated company. A major action taken to support this was the internal
development of an integrated global sourcing process, which the company
refers to as its Global Engineering and Procurement process (GEP). Global
engineering and procurement focuses on specific global applications as identified
by an executive steering committee.
Each new production facility (built as a stand-alone plant or built onsite to
feed a customer’s plant with industrial gases) now involves an extensive
analysis between US and UK design centres to identify areas of commonality,
standardisation, and synergy in procurement and design. Cross-functional
teams, with representatives from the US and Europe working jointly, develop
common specifications and contracts that satisfy each centre’s needs while
supporting future replacement and maintenance requirements [11].