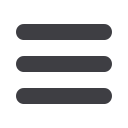

Mechanical Technology — August 2015
11
⎪
Proactive maintenance, lubrication and contamination management
⎪
After starting the process manually, the plating is mechanised by attaching
the two plating shoes to a rotating beam. The total electrical energy in kWh
is used to determine the coating thickness for a given area to a thickness
accuracy of better than 99%.
The journal-bearing surface of a shaft coated with a nickel cobalt
hardened layer.
Refurbishment of the Transnet trac-
tion motor casings can be done with
the with field coils intact and the
change in coating area around the
profile (left) is easily accommodated
by the process.
damage will be cut away before a new
section is welded on. This has potential
consequences with respect to distortion
and may potentially affect the current
carrying capacity.
“Using our cold selective electroplat-
ing process, however, we can take all
of the necessary equipment onto site
and complete the repair
in situ
. Without
dismantling anything at all, we will build
up the damaged aluminium section and
we can then coat the surface with silver.
I am certain that we can do this job at a
fraction of the cost of sending the whole
component out for a traditional repair,”
Pienaar reveals.
The equipment needed is relatively
simple: a dc rectifier; the anode ap-
plicator with its copper shoe and felt
covering; a solution tray to capture and
recycle electrolyte; a small variable flow
pump to recirculate the electrolyte; and
the electrolytic solution itself. For coating
circular components, it is also possible
to automate the process to some extent,
by rotating either the component or the
shoe so as to maintain brush-like contact.
The plating control unit is equipped
with an amp-hour meter with a six-digit
impulse counter to ensure precise plat-
ing deposits. Pienaar explains: “The
deposition rate for this process is directly
proportional to the current density. This
is because there is an exact relationship
between the number of electrons flowing
into the cathode and the amount of metal
deposited. The total electrical energy in
kWh therefore relates directly to deposit
volume, so it can be used to
determine the coating thick-
ness for a given area.
“We have developed plat-
ing characteristic data for all
of our electrolytes and, for
any given application, these
can be used to determine
the quantity of electrolyte
required, the plating current
and voltage and the total
energy required to achieve the neces-
sary thickness. On a 100
µ
m thickness,
we will be accurate to within 0.01
µ
m
or within 99% of the specification,” he
assures, adding that no post finishing is
required once the process is completed.
“The finished surface does not look as
bright as those coated in an electroplating
tank, but measurements show that the
selective electroplating process produces
higher surface smoothness than tradi-
tional electroplating.”
In addition, all the electrolytes are
manufactured in South Africa and the
intellectual property associated with
the characteristic data is South African
owned. “But the idea is not to sit on this
technology as an exclusive service pro-
vider. We aim to help small businesses to
set up local selective electroplating and
refurbishing services all over the country,”
Pienaar continues. “Cash flows in current
times are being squeezed and we believe
that greater access to this process can
save clients significant amounts of money
in the long term.
“On the Transnet traction motor
casings, with field coils intact, it costs
something like R100 000 for a strip out
and repair using fusion-based processes.
We are able to avoid having to remove the
coil while repairing the casing and journal
bearing bores, completing the equivalent
job at a fraction of the cost,” he says.
Of the six main Transnet workshops:
Koedoespoort, Bloemfontein, Durban,
Germiston, Salt River and Uitenhage
all have invested in their own selective
electroplating equipment. “We have
equipped these Transnet facilities with
the rectifier and rotating equipment
required and we supply the electrolytes
for them to refurbish all of their rail axles
for themselves.
“We see this as an ideal model to
take to other industries in South Africa.
Whether as part of small engineering
shops or as mobile service providers op-
erating onsite or out of containers, we see
this process as an ideal entrepreneurial
opportunity. As well as reducing main-
tenance costs for industry, the process
can help to create jobs and improve the
economy,” Pienaar concludes.
q