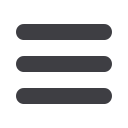

Mechanical Technology — August 2015
15
⎪
Proactive maintenance, lubrication and contamination management
⎪
Ultrasonic detectors can locate and quantify
compressed air, gas and steam loss to leaks
and faulty traps, passing process valves,
cavitating pumps, over lubricated bearings
and more.
"Training is the cornerstone of an effective ultrasound inspection program." Allan Rienstra, SDT North America Tom Murphy Our Level 1 & 2 Airborne and Structure Borne Ultrasound Inspector's courses are a 3-day comprehensive mix of theory and practical experience and provide maximum transfer of knowledge, skills, and abilities. User Group discussions for CBM Ultrasound users and Underground Tank Testing. Don’t miss this opportunity to work one-on-one with the worlds most experienced ultrasound trainers and inspectors. For further information and registration: www.martec.co.za• Tel.: +27 11 326 2708 • Cell: +27 76 903 7235 • Email: matthew@martec.co.za COURSE DATES UAS Software Training 31 st August & 1 st September Level 1 2 – 4 September 2015 Level 2 7 – 9 September 2015 Tank Test Training 7 – 9 September 2015 User Group 10 th September 2015untold stories of prospective clients, upon
being shown the latest offering, saying
something like “So that is what that
thing is!”. Invariably this is followed by
scratching through a cupboard in a back
room somewhere, dusting off an infra-red
camera, vibration analyser or ultrasonic
detector with long-dead batteries with an
“Aha! I thought I saw one of those here
somewhere.” At this point the salesman
knows he is in for a hard sell. Any one
or more of the reasons mentioned above
will have tripped up the organisation and
experience will be negative. So how do
you prevent yourself (and your organisa-
tion) from falling into the same hole, or
getting out of it if you are already there?
Getting out is worse!
As always, the key lies in careful
research and planning. Do your home-
work. Know where you want to get to.
Identify and anticipate the hurdles and
don’t underestimate them. Ensure there
is visible management support and com-
mitment. Build a solid foundation. Look
for the quick wins that are meaningful
and will give the initiative the boost it
will most certainly need. But, you might
ask, where to look and for what? So let’s
consider what could make for meaningful
quick wins in today’s economic climate
and business landscape.
First, be reminded that predictive
maintenance starts with condition
monitoring, but there are two aspects
to plant condition. The most common is
health status, which is linked to reliabil-
ity. This is very, very important and is a
foundational pillar supporting predictive
maintenance, but there is another that
is often overlooked and can be the key.
This is plant performance. When plant
performance is routinely measured and
monitored as part of the production
process it is automatically taken care of.
Deficiencies show up quickly and the
need for corrective action is obvious and
usually taken care of.
However, when aspects of plant
performance are not routinely measured
and monitored and deterioration occurs,
the consequences can be very significant
and nevertheless go undetected. This is
because many degradation processes are
slow and insidious. The worst is when
the deterioration leads to rising operat-
ing costs that eat into the bottom line to
an ever increasing degree. The effects of
reducing efficiency can be particularly
pernicious, especially when it occurs in
items like pumps, fans, compressors,
boilers and their associated distribu-
tion networks. In these situations it is
not unusual to find that, eventually, the
avoidable energy loss exceeds the energy
consumed. The cost to the organisation,
the environment and the country is huge.
In addition, plant in this inefficient state
requires more maintenance and is less
reliable.
So – the quick wins we are looking
for lie right here.
Think thermography
to detect faulty
steam traps, heat loss to defective or
inadequate lagging, overheated bearings,
motors with bad cores, heat loss and
leaks in buildings.
Think ultrasonic detectors
to locate and
quantify compressed air, gas and steam
loss to leaks and faulty traps, passing
process valves, cavitating pumps, over
lubricated bearings and more.
Most findings in the above categories
are associated with quick, easy and low
discovery costs. Similarly the corrective
interventions are usually simple and low
cost, yet yield significant benefits. These
are quick wins that will easily earn rec-
ognition and support by rapidly helping
your organisation’s bottom line.
These two technologies are so well
suited to finding low hanging fruit be-
cause of their versatility. Look for this
when evaluating your starting point and
consider both plant health and perfor-
mance. With many strings to your bow
you are a lot more likely to hit a target
that will add value and put you on a
sound footing.
q