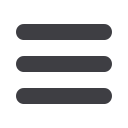

18
Mechanical Technology — August 2015
⎪
Materials handling and minerals processing
⎪
M
ark Sheward, sales man-
ager of mine shaft systems
for FLSmidth, says that
the Platreef minewinder
engineering contract award was based on
the company’s 60-plus years’ of experi-
ence and an extensive reference base of
installations. The largest Koepe winders
previously supplied by FLSmidth are the
two 6.5 metre diameter units at Impala
16 shaft and their successful implemen-
tation forms the basis of the design and
engineering undertaken for the Ivanplats
Platreef Project winders.
“Experience is critical in projects of
this nature and the ability to adapt to
changing conditions is one which differ-
entiates FLSmidth. Each of the two 6.0 m
diameter Koepe winder installations with
drums, brake systems and drives needs to
be accommodated within the constraints
of the headframe dimensions. The solu-
tion we provided involved installing the
two Koepe winders at 90° to each other,
with the auxiliary winder being installed
on a lower level,” Sheward explains.
During the early engineering phase,
To facilitate the design of the headframe structure by Murray & Roberts
Cementation, FLSmidth has recently completed the early engineering contract
for the production, service and auxiliary winders for Ivanplats Platreef
Project No 2 Shaft. The solution involves two 6.0 m diameter Koepe winder
installations at 90° to each other, with the auxiliary winder being installed
on a lower level.
The Ivanplats Platreef production and service winder engineering solution involves two Koepe winders at 90° to each other.
The FLSmidth 6.5 m Koepe Winders at
Impala 16 Shaft showing the 90° orientation
for space saving.
Early engineering for Ivanplats Platreef
FLSmidth made use of Finite Element
Analysis (FEA) to establish and verify
the stress loading in the final design.
Other supplied data included dimensions,
loads, required tolerances, stiffness re-
quirements and the position and length
of the anchor bolts, as well as the mass
and dimensions of the major components
to be lifted into the headframe.
Both the production and service wind-
ers are four rope friction winders. The
production winder will hoist two 40 t
skips, while the service winder will be
equipped with a man/material cage and
counterweight. The rock or production
winder is being designed for a rope speed
of 18 m/s while the man/material winder
will operate at 10 m/s. The auxiliary
winder, with a rope speed of 6.0 m/s, will
be a 2.4 m diameter, 1.2 m wide single
drum unit and could initially be ground-
mounted and used for shaft equipping
before being relocated to the head frame
on completion of shaft sinking.
The shaft depth is approximately
1 050 m and braking will be effected
on all three winders by a four-channel
closed loop hydraulic system incorporat-
ing disc brakes.
New small winder design
The auxiliary winder forms part of
the new small winder design, which
FLSmidth has been developing over the
past year. This ongoing development
work allows design optimisation and a