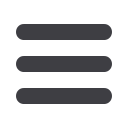

Metal
Protection
Tubes
Technical lnformation, Applications,
and
Suggestions
Illletal
Protection
Tubes'
Some General
Suggestions For Effective
Metal
Protection
Tube
Use:
/
Carelully select
the proper
protection
tube
alloy
for your
process
to
maximize
the service
life.
{
tilse a thick
walled tube,
such as
schedule
80, double
extra
heavy,
or
Richards heavy duty SP size
for
longer
service
life.
{
tlse
a
thin
walled
tube, such
as schedule
40, or
smaller O.D.
tube,
if
you
require
a
quicker
temperature
response time.
/ t
tne
protection
tube will
be subject
to severe
mechanical shock
or abrasion,
use
the
Richards heavy duty
SP
size.
/
Protection
tubes should be inserted
into
fluids a
minimum
of
six
times the
O.D.
of
the tube.
/
Protection
tubes should be inserted
into
gases a
minimum of
eight
times
the O.D.
of
the
tube.
/
lnsertion
lengths for
furnaces and salt
baths are
typically a
minimum
of 6"
(152.4mm).
/
Protection
tubes, which
pass
through a
hot
zone
(muffle
furnace), should
be inserted
at least
12" (304.8mm).
/
ln
molten
salt
baths, angle assembly
tube
lengths
should
be
a
minimum
of
18",
to
protect
the
elbow
from
level changes.
/ t
tne
elbow
on
angle assemblies
will
be subject
to
high
temperatures,
an
all alloy
bent type
tube should be
used.
/
neptace all
metal protection
tubes
on
a
regular basis, since they
will become become
porous over time.
/
Never shorten
the
life
of
new
thermocouple
elements by placing
them
into old,
worn-out, porous,
protection tubes
/
Protection tube overall lengths should be long enough
to
insure that
the
head temperature
will
not exceed
400"For
2O4"C.
{
tlse
large O.D. or
thick walled
protection tubes
where sagging
is
a
problem
at
elevated temperatures.
/
trlote
that
metal tubes are somewhat porous
above
1500"F or
815"C,
so in some cases a
ceramic
inner
tube
is
also
used.
Norninal
Pipe
Size
Dimensions.
t
H
H
1/8"
.41
10.4
.27 .068
6.9
.22 .095
5.6
114"
.54
13.,,7
.36
.088
9.1
.30 119
7.6
lld
3/9
"
.68 1V.2
.49
.091
12,4
]Fil
.42
.126
14.7
112"
.84
21 .3
.62
.1
09
15i,.7
m
.55
.147 14.0
.466
.187
11 .B 4'.7
4
.25 .29
6.4 7.37
314"
1.05
26,,7
.82 113
24.8
tEt
.74
.154
18.8
.614
.218
15.6
5.53
.43
.31
10.9 7,87
1"
1.32
33,5
1.05
.1
33 26,7
FI
.96
.179 24.4
.815
.250 20.7 6,35
.60 .36 15.2
9.14
1
114"
1
.66
42,.2
1
.38
.140
35.1
E
1.28
.191
32.5
l
1
.16
.250 29.5 6.35
.90 ,38
22.8 9.65
1
112"
1
.90
48.3
1
.61
.145 40.9
3qt
1
.50
.200
38.1
1.34 .281
34.0 7.13
1.10 .40
27,9 10.16
2"
2.38 60.3 2.07
.154
52.6
H
1.94
.218 49.3
1.69
.343
42.9 8.71
1.50 .44 38.1
11
,18
2112"
2.88 73.0 2.47
.203
62.7
E
2.32 .276 59.0
d
2.13 .375
54.1 9.,52
1
.77 ,55
45.,0
13.97
3"
3.50 88.9 3.07 .216
77,9
lFt
2.90 .300 73.7
2.62
.438
66.5
11
,12
2.30
.60
58.4 15.24
3112"
4.00
101 .6
3.55
.226
90.1
ffi
3.36
.318
85.4
2.73
.64
69.3 16,26
4"
4.50
1:14.3
4.03 .237 102.3
@t
3.83 .337 97,2
s,56
|
3.44
.531
87.4 13.48 3.15
.67 80.1
17.O2
Page'82