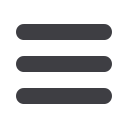

98
July 2013
Article
What drives choices regarding
pipe material?
By Chris Ricketts, category director, BSS Industrial, UK
Value engineering has traditionally been a tool reserved
for larger scale commercial projects, but the struggling
economy means that cost cutting is now an integral part of
any construction plan. Rather than a post pricing activity as
historically been implemented, value engineering is being
employed up-front, pre-submission of pricing to clients.
Whilst other areas of a build are easily value engineered to
introduce more cost effective suppliers and an alternative
product, the piping systems industry has seen more complex
changes, which take the overall cost of an installation into
consideration, rather than just the initial cost of purchasing
the material itself.
That said, there are still a number of instances where a simple
change in material can aid a cash strapped building project.
Cost stability
For many years, habitual specification
has meant that copper was often the
material of choice for hot and cold water
systems, but this is changing.
The volatile price of metal can now
cause major discrepancies in quantity
surveying, with price fluctuation changing
the cost between the time of specification
and purchasing. This uncontrollable price
increase has made piping systems a key
area of consideration for those in charge
of value engineering.
It also means that finding an alternative
material that can deliver savings can be
imperative to a successful project.
When exploring the various drivers behind the
specification of piping systems, it seems that cost still
reigns as the determining factor.
However, it is not just the cost of the material itself,
but the cost of the overall installation that needs to be
calculated.
Chris Ricketts, BSS Industrial category director, explains
how value engineering is shaping trends in piping sales
and how money is being saved on-site.
As the cost of metal remains unpredictable, there is a visible
trend in material substitution in order to bring cost stability to
the specification process.
Copper is a ‘one material fits all’ product and is suitable for
a wide variety of building services piping applications, so the
process of value engineering this particular aspect of a build
isn’t straight forward.
More often than not, the copper in a specification will need to
be replaced with a number of different substitutes to suit the
variety of piping systems in the project.
Although this sounds time consuming, it is a worthwhile task
and extensive cost savings can be made by switching to
alternative piping and jointing systems such as press fit and
grooved jointing solutions.
Initial outlay vs overall cost
Switching to a cheaper material might seem like the obvious
solution, but value engineering managers are looking at the
bigger picture to ensure that savings are maximised.
Other considerations for the installation include fittings and
joints, labour costs, on-site insurance, health and safety
implications, flushing and cleaning cost and completion times,
which can all result in substantial cost savings which outweigh
the initial outlay cost of a more expensive material.