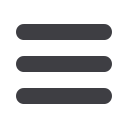

Industry News
www.read-tpt.com12
J
uly
2013
Specialist Nadcap accreditation
for welding
FINE Tubes, a manufacturer of precision
metal tubing, has been recognised for
its on-going commitment to quality and
continual processes improvement by
receiving the latest NadcapAccreditation
for Welding.
In meeting the stringent requirements
of Nadcap accreditation, Fine Tubes
has demonstrated its commitment to
achieving the highest quality standards
by satisfying customer requirements
and industry specifications.
“Fine Tubes continually strives to
enhance its special processes. Thus, in
achieving this high-status accreditation,
we have improved various areas of our
welding procedures,” explained Rob
Eatwell, quality assurance manager
at Fine Tubes. “The process controls
were consolidated and formalised into
documented PCMs which generated a
formal approval process for weld mill
operators and inspectors. This has led to
improved training and awareness of the
whole weld mill and technical teams.”
Specifically, the Nadcap accreditation
allows Fine Tubes to conduct
longitudinal fusion welding of tubes and
entitles the company to appear on the
Quality Manufacturers List.
Mr Eatwell added, “Fine Tubes are
now on the Nadcap accredited special
process list for welding – joining our
heat treating and NDE qualifications.
Quality is at the foundation of all our
operations and this will help to cement
customer confidence in our tube
welding processes as we aim to exceed
industry standards.”
Joe Pinto, vice president and chief
operating officer at the Performance
Review Institute, commented, “Achieving
Nadcap accreditation is not easy: it is
one of the ways in which the aerospace
industry identifies those who excel at
manufacturing quality product through
superior special processes. Companies
such as Fine Tubes work hard to obtain
this status and they should be justifiably
proud of it. PRI is proud to support
continual improvement in the aerospace
industry by helping companies such
as Fine Tubes be successful and we
look forward to continuing to assist the
industry moving forward.”
Fine Tubes has a fully integrated
facility for the manufacture and the
research and development of high
quality precision tubes in seamless,
welded, and welded and drawn forms.
The company manufactures high
precision tubes in stainless steel, nickel,
titanium and zirconium alloys, and the
standards and specifications for these
tubes and coils are extremely high,
aimed at applications in the most hostile
operating environments. Fine Tubes
products serve a wide range of markets
such as the aerospace, medical, oil and
gas, nuclear and power industries.
Fine Tubes Ltd
– UK
Fax: +44 1752 733301
Email:
sales@fine-tubes.co.ukWebsite:
www.finetubes.co.ukUS premiere for KraussMaffei
THE KraussMaffei Corporation (USA)
kicked off 2013 with a US premiere. The
GX series was presented for the first time
in operating mode to a wide audience of
experts during a “TechDay”. This event
was held at the plant in Michigan, USA
together with Proper Group International,
the cooperation partner for mould and
process technology.
KraussMaffei presented a GX 400-
4300 in operating mode during the world
premiere. In particular, customers from
the automotive and packaging/logistics
industries reacted very positively to the
new GX series, which is suited to many
different injection moulding processes
thanks to its efficiency and extensive
catalogue of options as a basis.
The GX series currently covers the
clamping force range from 4,000 to
6,500kN in different sizes and equipment
variants for production requirements in
a large number of industries. The GX
machines are impressive during the
production of free falling packaging/
logistics parts for the automotive industry
or the consumer goods sector.
“We received a large number of
orders for machines last year, a fact
which proves that the American market
developed very positively,” said a
spokesman. “We have made a good
start to the current fiscal year thanks
to the continually high demand for our
products and the very positive feedback
from our customers regarding the quality
of our machines and service.” The
company, which has been operating
in the USA for more than 45 years,
systematically acquired this status over
a long period and also geared its product
and service portfolio to this market. The
result is a complete range of machines
with clamping forces between 350 and
40,000 kN, including ideally adapted
automation solutions. “The technology
supplied by KraussMaffei corresponds
precisely to the requirements of our
customers on the American market,”
added the spokesman. “We have
categorically proved this today through
the live demonstration of our machines.”
Visitors to the plant in Warren were
also able to see an all-electric AX 180-
380 and a MXZ 1600 multi-component
machine in operating mode.
“The SkinForm procedure is used to
produce premium quality polyurethane
surfaces on thermoplastic carriers
in a production cell. The technology
competence of KraussMaffei can be
clearly seen here throughout the entire
process chain,” said Frank Peters, vice
president sales injection molding and
machinery at KraussMaffei. “We supply
machines, automation technology, mould
technology and the trim solution, which
are all based on our expert knowledge.”
In the USAKraussMaffei Corporation and
Proper Group International in Warren
(Michigan) have been cooperating since
2010 as part of a strategic partnership
for turnkey solutions for processing
polyurethane. Both partners also use the
advantage of the joint technology centre
in Warren where KraussMaffei injection
moulding machines with a clamping
force of 800 and 27,000 kN are available.
KraussMaffei Corporation
– USA
Website:
www.kraussmaffeigroup.com