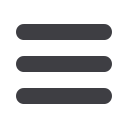

Industry News
www.read-tpt.comJ
uly
2013
13
Increasing levels of automation
LANDER Automotive Ltd produces a
wide range of tube products for OEMs
and Tier One customers.
Founded in 1877 as W Lander & Sons,
the bending and welding technology
used to manufacture various wire goods
was later applied to tube, and in the
1950s the company began supplying
the UK automotive industry with bonnet
props, linkages and headrests. This
culminated in the change of name in
1991 and re-location a year later to
purpose-built premises.
In 2007 the company decided to sell
its subsidiary factories in Hungary and
Germany and to concentrate on creating
a ‘high quality, low cost’ design and
manufacturing centre of excellence in the
UK, focusing resources solely on tube
manipulation and cellular robotic welding.
Tube manipulation within Lander
Automotive is a mixture of single piece
manufacture and integrated cells
featuring bending and end-forming
machines supplied by BLM Group.
These include Smart all-electric CNC
tube bending machines, AST Tube-
Form ELE all-electric CNC tube end
forming machines and AST 30 tube end
forming machines.
“BLM is very strong on tooling design
and has products that complement our
lean manufacturing requirements,” said
Roger Whitehouse, Lander Automation’s
managing director. “We benefit from
flexibility in terms of right- and left-hand
bending on the same machine; relatively
fast changeover times; and the capability
to produce single parts in sequence
ready for assembly on the line rather
than in batches. Take underfloor heating
pipes as an example: we make small,
medium and large assemblies in that
order, because one of each is needed for
each vehicle build.”
“We have progressively increased the
level of automation within the factory,
and there are now 40 robots involved
in welding, materials handling and
machine load/unload.
“Adaptability to future requirements is
also crucial. We are subject to vehicle
life cycles, so as contracts come to an
end we have to bring in replacement
business, and to adapt quickly to
changing production requirements as
well as the inevitable on-going schedule
changes. We buy BLM machines
not just for current contracts but for
the ones after that, so performance,
flexibility and reliability are key criteria.
Energy efficiency, too, is very important
to us, hence the attraction of all-electric
rather than hydraulically powered
machines.”
Suitable for bending tubes up to 28mm
diameter, BLM Group’s Smart all-electric
(8 axes) CNC tube bending machines
are programmed via proprietary VGP3D
graphical interactive software.
BLM Group UK Ltd
– UK
Email:
sales@blmgroup.uk.comWebsite:
www.blmgroup.uk.comLander Automotive Ltd
– UK
Email:
enquiries@lander.co.ukWebsite:
www.lander.co.uk