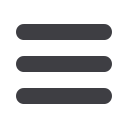

40
J
uly
2013
Technology News
Messe Düsseldorf GmbH
Postfach 101006 _ 40001 Düsseldorf _ Germany
Tel. +49(0)211/4560-01_Fax +49(0)211/4560-668
www.messe-duesseldorf.deDüsseldorf Houston Suzhou
São Paulo
Shanghai
Bangkok
Southeast
A S I A
Moscow Dubai
Mumbai
j o i n t h e b e s t
w o r l d w i d e
Tube Düsseldorf:
Innovations go global
Take advantage of the highest calibre expertise of the
No. 1 international fair as the show goes global. Draw
on international synergies from these leading trade fairs.
A cycle of regional events, staged in succession around
the globe, responding to local market and customer
needs. Detailed information on the full programme can
be found at:
www. t ube . de
tub1402_WW_87x260+3_INT.indd 1
14.02.13 08:30
Inclined is the
new trend
THE only manufacturer of railway wheels in the Ukraine
followed the worldwide trend in sawing large billets and relied
on the type KSS 1600 inclined bed saw from Linsinger. This
year in April a machine fully equipped with a material handling
system was supplied to the customer. The total weight of the
system designed for a hard 3-shift operation is 115 tons.
The concept of this inclined bed saw is based on integrating
the advantages of horizontal and vertical sawing machines.
The benefits quickly become clear when sawing large
diameters. The sturdy, 3-point workpiece tension and the
extremely quiet and vibration-free run of the saw guarantee a
long tool service life.
Eleven inclined bed saws are already in use in Russia and
the CIS states. Railway wheel manufacturers such as Vyksa
Steel Works, NTMK Nizhny Tagil and NTRP Dnepropetrovsk
are some of Linsinger’s customers.
The orders allocated for wheel saws in the past years
throughout the world were awarded to Linsinger, which is a
confirmation of its consequential further development.
The ongoing costs for tools, calculated over the service
life of the machine, make up several times the procurement
costs of the machine. A lot of money can be saved in this
area, but it can also be wiped out as well. Linsinger offers
tools manufactured in the company so that customers are
spared nasty surprises. These are aligned to the machine
when it is commissioned on Linsinger’s premises. Tests after
commissioning on the customer’s premises are therefore not
required and production can start running with the agreed
performance in the shortest time.
The development of new tool technologies is also one of
Linsinger’s concerns. The development of the Lincut
®
disc
miller with screw connected carbide inserts sounded a new
era in sawing. The panels achieve the longest life time thanks
to the coating, they are easy to replace and help to significantly
reduce the ongoing operating costs. This means, for example,
that the costs per cut for a diameter of 450mm are just €2
(tool costs only). An added benefit is that the procurement and
operating costs of a sharpening centre are avoided.
Three years of practical experience with the Lincut
®
side
milling cutter confirm Linsinger’s path of success. More than
40 Linsinger sawing systems with Lincut
®
are now in operation.
Linsinger
– Austria
Website:
www.linsinger.com