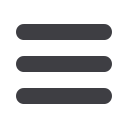

Technology News
www.read-tpt.com44
J
uly
2013
Tumble belt blast
machine
VIKING Blast & Wash Systems has
released a redesigned tumble belt blast
machine – the 12 cubic foot model 1200.
The latest version incorporates changes
to the loader and discharge belt options
that make it more durable in heavy duty
and foundry operations.
The increased options make the 1200
a more versatile machine, providing
wider applications to the many industries
served.
The new 1200 has a smaller footprint
by the integration of themedia lift system
and the elimination of the auger, which
lowers overall maintenance cost and
improves component accessibility. The
repositioning of the 25HP VKPowerMax
series blast wheel optimises the blast
pattern to make efficient use of wheel
performance.
The drum heads and
side liners are manganese
alloy as standard and easily
serviced. Other optional
features include rotary
scalping drum for removing
debris from blast media,
loader, take away belt, and
auxiliary abrasive hopper.
Front
bucket
loaders
and custom unloading
conveyors are common options for the
1200.
Peening requirements are satisfied
with optional variable speed blast wheel
control, electro magnetic abrasive
control valve and classifier, as well as
optional PLC and touch screen for pre-
programmed, recorded, part-specific
recipes.
All Viking cartridge style dust
collectors are sold with NFPA required
deflagration panels as standard.
Viking Blast & Wash Systems
– USA
Fax: +1 316 634 6658
Email:
sales@vikingcorporation.comWebsite:
www.vikingcorporation.comA non-chlorine alternative
QUAKER Chemical continues to
expand its front to back product
offerings for the tube and pipe industry,
now into precision seamless tube
manufacturing.
Quaker Chemical’s cold pilger
lubricants, ATLAS™ 3374-140 and
ATLAS™ 3374 – DPX, provide an
alternative to the traditional chlorinated
paraffin containing products for
lubrication in the pilgering process.
These two products were formulated
together and designed to be fully
compatible for internal and external
lubrication.
ATLAS 3374-140 and 3374-DPX have
successfully replaced their predecessors
and can be applied on stainless steel
as well as on duplex alloys, since the
products are non-chlorine containing
and provide extreme pressure (EP)
lubrication through sulphur.
The ATLAS 3374 brand provides
an alternative that not only maintains
productivity, but also easy disposal.
Other advantages from this product
line are secondary tool wear, high
temperature resistance, and suitability
for stainless steel deep drawing.
Quaker Chemical is a global
provider of process fluids, chemical
specialities, and technical expertise
to a wide range of industries,
including steel, aluminium, automotive,
mining, aerospace, tube and pipe,
cans, and others. For nearly 100
years, Quaker has helped customers
around the world achieve production
efficiency, improve product quality,
and lower costs through a combination
of innovative technology, process
knowledge, and customised services.
Headquartered in Conshohocken,
Pennsylvania, USA, Quaker serves
businesses worldwide with a network
of
dedicated
and
experienced
professionals whose mission is to make
a difference.
Quaker Chemical
– USA
Website:
www.quakerchem.comViking Blast & Wash Systems
1200 belt blaster
Quick tooth
check device
SWISSCUT SW Wil produces HSS,
TCT and friction saw blades.
The company is also a major
re-sharpener of saw blades in
its home market in Switzerland,
re-sharpening more than 40,000
blades each year.
SW Wil sells not only saw
blades, but also cutting technology,
providing customers with a complete
package.
The company decided to build
the QTC (quick tooth check) device
after observing that, in many cases,
customers did not get the same
cutting performance after performing
their own in-house re-sharpening.
Customers were asking for a
control unit, but there was none on
the existing market, or the cost of a
unit was too high.
The aims of making a control unit
were clear: low cost, simple to use,
and fast operation.
The QTC unit performs shape
control in a first step, and angle check
in a second step.
SW Wil
– Switzerland
Fax: +41 71 911 49 32
Email:
swwil@sw-wil.comWebsite:
www.sw-wil.com