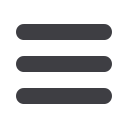

Bending, end forming
and
swaging
www.read-tpt.com86
J
uly
2013
New bending technology for tube
ACCORDING to estimates by the
International Energy Agency (IEA), the
energy demand of the world population
will increase drastically in the coming
years: in 2030, around 5.5 billion people
will have access to the electricity supply
– this is equivalent to growth of 1.5
billion consumers within only slightly
less than two decades. To meet the
increased energy demand, in addition
to investment in renewable energies,
the construction of new power plants
and modernisation of existing facilities
in particular are vital. One critical
criterion here is to significantly improve
efficiency in the power plant process.
The requirements for the installed
tube systems and tube materials are
therefore also increasing, as they make
a noticeable contribution to increasing
efficiency.
Schwarze-Robitec
has
developed special bending machines
for precisely this application area, which
bend high-strength, thick-walled high-
pressure tubes as well as boiler tubes,
tube coils and entire membrane tube
walls accurately and both time and cost-
effectively.
The requirements for liquid and steam
line systems in modern power plants are
increasing: significantly higher pressure,
flow and temperature values result in
increasing strain on the systems. At the
same time, the legal constraints and
requirements are intensifying. Leakages
can result for example in costly repairs
or – which is worse – investigations,
fines and even a deactivation order from
the relevant regulatory authorities. This
makes the use of durable, safe and
effective tube systems and solutions
all the more important. Whereas thick-
walled high-pressure tubes and pipes
have been welded together for decades
from various straight and pre-bent tube
components, modern tube bending
processes offer significant advantages
with respect to safety, subsequent
maintenance and the requirements of
the present tube parameters as well
as appreciable benefits in terms of
manufacturing costs and times.
The semi-automatic SR 320 tube
bending machine and the automatic
CNC 320 HD from Schwarze-Robitec
GmbH produce complex tube systems
in one operation from a single tube, for
example for pressure and steam lines,
manifolds and similar tubes. Being
equippedwithspecial tools, themachines
bend thin and thick-walled tubes with a
maximum diameter of 323.9 x 17.5mm.
With a tube size of 323.9 x 10mm,
for example, they have no problem
producing a bending radius of 1.5 xD,
which is equivalent to a bending radius
of 485mm in the example mentioned.
The semi-automatic machines in the
SR series are particularly suitable for
the production of single bends and
small series. The automatic, CNC-
controlled machines are also suited to
complex tube systems
with several bends
or large batch sizes.
“Compared with the
induction
bending
processes, our cold
bending process offers
huge time savings
in the production
process,” Schwarze-
Robitec plant manager
Jürgen Korte explains.
“Whereas hot shaping of these work
pieces takes around eight hours, our
customers require an average of only
six minutes for one bend.” Depending
on the specific application, Schwarze-
Robitec offers the machines from their
heavy duty machine series for various
diameters and wall thicknesses up to
610 x 21.4mm.
The machines are available in semi-
automatic design with SR control and in
automatic design with CNC control. All
machines can be equipped with a tube
magazine and tube feed and enlarged
up to fully automatic bending cells.
Very different but similarly exacting
requirements now also exist for boiler
tubes and tube serpentines in power
plant construction. The production of
smaller boilers with greater capacity, for
example, requires the use of extremely
tightly bent tubes. Depending on the
tube diameter, it is not uncommon for
the required minimum bending radius to
be 1xD (sometimes under 1xD).
The semi-automatic booster bending
machines and automatic CNC pressure
bending machines from Schwarze-
Robitec are designed precisely for these
requirements.
The unique cold-bending process
from Schwarze-Robitec offers utmost
precision and surpasses the tolerance
requirements for wall thinning and out-
of-roundness of European standard EN
12952, American Society of Mechanical
Engineers ASME B31.1 and all other
international standards. The CNC-
controlled booster bending machines
are also equipped with a tube positioning
device, which facilitates fully automatic
bending of tube systems. For efficient
processing of very large and complex
tube serpentines, Schwarze-Robitec
offers the CNC Twin series machines:
this machine series, which is available
in three different sizes up to diameter
88.9 x 11mm, uses two vertically and
horizontally movable bending heads (1x
left-bending, 1x right-bending), which
alternately bend the tube clockwise and
anticlockwise.
Consequently, the tube serpentine
does not need turning after each bend,
which ensures quick and economical
production
processes
and
the
manufacture of large leg lengths.
Schwarze-Robitec GmbH
– Germany
Email:
sales@schwarze-robitec.comWebsite:
www.schwarze-robitec.comThe CNC 100 DB Twin booster machine
The FL 3600
tube bending
machine