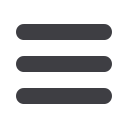

this is the case, wouldn’t this be a step
backward instead of the next phase of
a technological evolution?
There’s room in the discussion for
another perspective of Industry
5.0. In this view, as increasingly
sophisticated artificial intelligence (AI)
algorithms become commonplace,
there is a potential to enhance
machine-to-machine communications.
For instance, if a machine in a factory
cell becomes limited in its function,
another machine in the cell can
automatically take over to perform
the stalled machine’s task while
still supporting its own main task.
This capability, or nimbleness, of
the manufacturing line to keep it up
and running will foster a new breed
of underlying ICs that provide a
higher level of flexibility to adapt its
functionality to the requested task at
hand. At Tesla’s Fremont production
plant, human workers are currently
alerted by flashing red and yellow
lights when a particular robot needs
maintenance. But in the future, we
may see more automated factories
where the robots require much less
human intervention when one unit
goes down for repairs. This self-aware
digital factory approach does have
implications on the human workforce,
but, again, it’s a shift that began as
Industry 4.0 matured.
Smaller and Smarter
While machines handle repetitive and
physically taxing tasks, people would
service or repair the machines…
and design them. As AI algorithms
evolve to become more accurate and
reliable, this will influence the need
for compact programmable logic
controller (PLC) modules that provide
universal IO capabilities to drive the
industrial internet of things (IIoT) to
the next level of dynamic control. One
technology that provides facets of
this universal IO capability is IO-Link.
This powerful point-to-point serial
communications technology provides
flexibility to interchange sensors via a
common physical interface, creating a
number of software-defined sensors
based on the IO Device Description
file. The IO-Link port then serves as
a universal IO that can turn into any
type of sensor, so a factory worker can
remotely reprogram these intelligent
sensors to handle changed or new
manufacturing requirements.
Sensors provide input stimuli (as
analog voltages and currents as well
as digital IO) while the PLC interprets
these inputs to establish the
operational conditions of the factory
in its environment. Based on these
conditions, the PLC must accurately
make decisions to instruct the array
of actuators to enable adaptive
manufacturing, maintain throughput
to keep the factory up and running,
and provide the ability to improve the
operational production efficiency of
Image 3:
The Go-IO industrial IoT reference design drives intelligence to the edge.
34 l New-Tech Magazine Europe