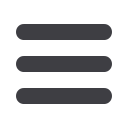

June 2015
AFRICAN FUSION
31
Performance
Tubular
Coated
Weldability
Excellent
Average/Poor
Heat Input
Extra Low
High
Spatter
Insignificant
High
Slag
Negligible
High
Slag Removal
Not required Essential
Deposition Efficiency High
Average/Low
Dilution
Low
High
Baking
Not required Necessary
WA tubular hardfacing electrodes (TEs),
while designed to be used in the same way and with the same
power sources as coated shielded metal arc electrodes, are
constructed like a cored wire electrode. The alloying constituents,
which are mostly metal powders rather than flux, are contained
inside the hollow electrode by an outer metal sheath.
electrodes
A comparison of the welding performance of tubular and
coated hardfacing electrodes.
distortion and a lowering of the risk
of burn-through. “These tubular elec-
trodes can be welded at low operating
currents, which allows less expensive
power sources to be used and, most
importantly, it allows thin sections such
as the flights of screw conveyors to be
hardfaced successfullywithout destroy-
ing the basic geometry,” he suggests,
adding that because of the spiral shape
of conveyor screws, these products are
not so easy to hardface using more au-
tomated processes.
While WA’s 6.0 mm tubular elec-
trodes have a steel stub, the larger
diameters use analuminiumstub, which
enables the stubdiameter tobe retained
at 6.0 mm, regardless of the electrode
size. This makes the entire range com-
patible with typi-
cal MMA electrode
holders.
The electrodes are
highlyalloyedanddense-
ly packed, with a thin steel
sheath, which requires low
amperage tomelt andsustain
an arc. “A key differentiating
feature for us is the green outer
coating, which is designed to offer ex-
ceptional moisture resistance,” Zylstra
believes. “This means that baking is no
longer required as the core ingredients
are not susceptible to moisture pickup
at all. This saves energy, processing time
and, therefore, money. It also makes
the electrodes ideal for use in humid,
outdoor environments,” he adds.
Describing the feel while welding,
Zylstra says tubular electrodes are
“feather-light”, which takes somegetting
used to, but the “weldability is excel-
lent”. Spatter is almost non-existent and,
because the core is mostly made up of
metal powders rather than flux, slag lev-
els in the deposit are low, requiring no
slag removal or grindingbetween layers.
Offering a 50% higher deposition
rate than coated SMAWhardfacing elec-
trodes, Zylstra points out that a further
niche advantage is the positional capa-
bility of tubular electrodes. “Because
the electrodes canbeweldedat currents
as low as 80 A (6.0 mm), our tubular
consumables can be used to hardface
in the vertical-up position (3G/3F),” he
assures. “This makes the range very
versatile, with down hand welding be-
ing possible at 120-130 A for the 6.0 mm
electrode and as low as 150‑160 amps
and 200‑220 A for the 8.0 and 12 mm
electrodes, respectively.
The product range
At the starting point of Welding Alloy’s
tubular electrode (TE) hardfacing range
are the primary chromium carbide
coatings (HC-TE and HC40-TE). These
electrodes produce a microstructure of
chromiumcarbides in an austeniticma-
trix. “Thesearehighchromiumcast irons
andwill produce stress relief cracks. This
is normal,” Zylstra suggests. “If no cracks
are produced, then something is wrong
with the hardfacing composition,” he
points out.
Typical uses include palmoil extrud-
ers, screw conveyors, gyratory crusher
cones and mantles, dredge pump bod-
ies, mining and earth moving equip-
ment, agricultural equipment, wear
plates, sugar mill crusher hammers,
drag line components, quarry and sand
handling equipment, and brick manu-
facturing equipment.
One step up in terms of metallurgi-
cal sophistication are the CN-TE and
the CNV-TE electrodes that are used
to deposit complex chromium carbide
layers that offer better wear resistance
at higher temperatures. The CNV-TE al-
loy, for example, maintains its abrasion
resistance at up to 600°C and is suitable
for use in boilers, sinter plant or for blast
furnace components.
A third alloy group, STEELCARBW25-
TE and STEELCARBW45-TE produce lay-
ers of tungsten carbide (WC) andFe-Cr-W
carbides in an austenitic matrix. “Many
will have seen tungsten carbideparticles
being dropped into a melted pool to
produce layers such as these,” Zylstra
recalls. “But the powders used in these
tubular electrodes are so fine that they
can’t be seen.”
Both these grades have very high
abrasive resistance, with the W25 grade
having slightly better impact resistance
than the harder W45 grade. Typical ap-
plication include materials handling
components in contact with medium to
fine ores, coal crusher blades, conveyor
screens, concrete mixer components,
woodchippingor crushingmachinecom-
ponents, and brick and clay mill augers.
Concluding, Zylstra says that tubular
hardfacing electrodes are ideal for use
on irregular shapes where out of posi-
tion welding is sometimes required, for
low volume applications or for applying
surface coatings on many small parts.
“They are typically suited to repairs of
worn coatings and for use whenever
the advantages of continuous welding
with cored wires cannot be achieved,”
he suggests.