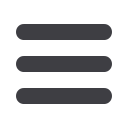

30
AFRICAN FUSION
June 2015
WASA: New tubular welding electrodes
W
elding Alloys’
core business in
South Africa is
hardfacing, cladding and
build-up repairs. “The dif-
ference between hardfac-
ing and cladding is simply
that hardfacing is about
depositing wear and abrasion resistant
materials, while the term cladding is
more commonly used to describe a
deposit that protects against corrosion,”
Zylstra begins.
Locally, WASA produces tubular con-
sumables and flux-cored welding wires
and is the only tubular wire consumable
producerinAfrica.“Wemanufacture60to
70 t of product per month, of which 50%
is used by one of our own Group compa-
nies, Apex Benoni, where we refurbish
crushing components and produce CrC
overlay plates for wear applications on
southern African mines,” he adds.
Briefly summarising the history of
tubular electrode development, Zylstra
says that the first patent for an arcweld-
ing process using ametal electrode was
awarded in 1892 toCL Coffinof Detroit. A
few years later, in the 1900s, Oscar Kjell-
berg of Sweden invented the covered or
coated electrode by dipping bare iron
wire into a thick mixture of carbonate
and silicate deoxidants. This paved
the way for modern covered electrode
development.
The evolution of tubular electrodes
began some 60 years later with the
emergence of flux-cored and Innershield
welding wires. Welding Alloys was
founded near Cambridge in the UK in
1966 and began manufacturing cored
hardfacingwires a fewyears later. “Then,
in 2010, as part of Welding Alloys’ Green
Electrodeproject, thecompanyacquired
tubular hardfacing electrode manu-
facturing technology from a Malaysian
company and, in 2014, began manufac-
turing a successful range of formulations
of its own,” Zylstra reveals.
WA tubular hardfacing electrodes
(TEs), while designed to be used in the
same way and with the same power
sources as coated shielded metal arc
electrodes, are constructed like a cored
wireelectrode. Thealloyingconstituents,
which are mostly metal powders rather
than flux, are contained inside the hol-
low electrode by an outer metal sheath.
Why? The main advantage of using
a cored electrode is the smaller cross
sectional area of the conducting path.
“If you think of a coredwire, it has a thin
At an SAIW evening meeting held in May, Wiehan Zylstra (lef), technical manager of
Welding Alloys South Africa (WASA) introduced the company’s new tubular welding
electrodes for manual surface repairs and hardfacing of thin or small parts.
WA’s tubular electrodes can be welded at low operating currents, which allow thin sections such as
the flights of screw conveyors to be hardfaced successfully without destroying the basic geometry.
Also, because of the spiral shape of conveyor screws, these products are not so easy to hardface using
more automated processes.
A key differentiating
feature is the green outer coating,
which is designed to offer exceptional
moisture resistance.
WASA’s
new tubular hardfacing
metal sheath that needs to bemelted by
the welding current, instead of the rela-
tively thick solid wire,” Zylstra explains.
“To melt the thinner section, a lower
total current is required to achieve the
necessary current density. The cored
construction, therefore, offers lower
heat input and higher deposition rates
compared to solid wire electrodes with
flux coatings on the outside,” he says.
WA’s tubular hardfacing electrodes,
which range in diameter from 6.0 mm
in diameter to 12 mm, offer extra-low
heat input; low dilution and base metal
penetration; and smaller heat-affected
zones than any solid electrode equiva-
lents. “Low dilution is very important
when it comes to hardfacing. The more
the dilution, the more the alloying ele-
ments such as chromium, niobium or
vanadium become diluted by the base
metal, reducing the wear properties of
the hardfacing layer. We usually advise
depositing three full hardfacing layers to
guarantee the chemistry and properties
of thedeposit are fully achieved, but high
alloy content in the first layer can allow
acceptable properties to be achieved
using only two layers,” Zylstra advises.
A further advantage of the low
heat input associated with the tubu-
lar electrode construction is reduced