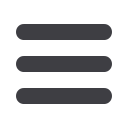

June 2015
AFRICAN FUSION
25
arc [9]. In the low-current case (170 A), globular transfer occurs.
As can be seen in Figure 2, the temperature distribution of the
MIG arc changes with the detachment of a metal droplet from
the wire tip. In contrast at the higher current (250 A), spray
transfer occurs. The liquid metal at the wire tip is elongated
toward the pool like sharpened pencil. The arc plasma shape
appears not to change, and its temperature field is less varied
bymoltendropbehaviour. Fluidity, surface tension and viscos-
ity of the liquid metal govern the shape and/or size of metal
drop at the wire tip. As is well known, the electromagnetic
force depends significantly on the current path flowing in the
liquid metal. This means that the shape of the arc plasma
touchedwith liquidmetal plays an important role on dynamic
behaviour of metal transfer.
In other words, the metal transfer mode is varied by
physical properties such as thermal conductivity and electri-
cal conductivity of the arc plasma. Accordingly, the composi-
tion of the shielding gas is one of the important variables for
controlling metal transfer. With this established, the change
in a gas shielded metal arc across a metal transfer cycle can
be predicted with aid of numerical simulation.
Concluding remarks
The essential components of the gas shielded arcwelding pro-
cess include theweldingmachine, electrodewire and shielding
Figure 2: Changes of the arc-plasma temperature field and drop shape for the open arc, argon-shielded GMAW process. (a): Welding current
of 170 A. (b): Welding current of 250 A.
(b) 250 A.
(a) 170 A.
gas. In addition to universities and national institutes, welding
machine makers, consumable makers and gas suppliers have
been putting effort into the research and development of de-
vices, consumables and newGMAWprocesses in collaboration
with various fabricators. Some of these developments have
been carried out based on visual observationwith recent high
performance digital cameras, along with knowledge derived
from numerical results of theoretical model.
References
1 H Maruo, Y Hirata, Y Noda: Quarterly Journal of the Japan
Welding Society, Vol.2 (1984) No.1.
2 H Maruo, Y Hirata: Quarterly Journal of the Japan Welding
Society, Vol.3 (1985) No.2.
3 H Maruo, Y Hirata: Doc.80-436 of Technical Commission on
Welding Arc Physics in Japan Welding Society(1980).
4 A Okada, H Yamamoto, W Nishikawa: Doc.80-437 of Techni-
cal Commission of Welding Arc Physics of Japan Welding
Society(1980).
5 T Ueguri, et al: Doc.80-446 of Technical Commission of Weld-
ing Arc Physics of Japan Welding Society(1980).
6 K Hashimoto, Y Hirata: IIW Doc. 212-1300-13(2013)
7 G Huismann: IIW Doc.212-952-99(1999).
8 K Himmelbauer: IIW Doc.XII-1875-05(2005).
9 Y Ogino, Y Hirata: IIW Doc.212-1324-14(2014).
GMAW: current progress