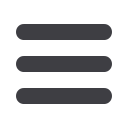

June 2015
AFRICAN FUSION
23
Figure.1: The change in bridge profiles after contact between a pendent droplet and a weld pool; (a): At an inclination angle of 0°. (b): At an
inclination angle of 45°.
is, essentially, a result of a lack of deep understanding of
welding phenomena.
Modelling and high performance control of
GMAW processes
The digitally controlledweldingmachine, as well as delivering
very fast and precise current and voltage control, now also
offers digitally controlledwire feeding, which has been consid-
ered a weak point in GMAWprocesses for many years, limiting
the use of the process for high performance applications. It
is now possible, however, for GMAW processes to become a
high quality welding process with an extremely stable arc –
equivalent to TIG welding arc – and simultaneously, a higher
productivity welding process because of its high deposition
rate. But in order to ensure the stability of the gas metal arc
is equivalent to that of the TIG arc, software is required to
continuously control welding phenomena and to provide the
optimum combination of current, voltage and wire feeding.
This means that information about the dynamic behaviour of
the arc, the electrode wire and the weld pool must be linked
to the control variables of the digital welding machine.
The computer technologies of today havemade rapid and
significant progress. They can nowbe used to carry outmodel-
ling and simulation of very complicated welding phenomena
with high temperature and high luminescence. Some predic-
tion about welding control phenomena are described here
basedon knowledge obtained through numerical simulations.
Figure 1 shows the change of a molten drop’s shape with
time calculated using a 3D numerical model just after contact-
ing the pool surface in the short-circuiting transfer process
[6]. In the case of a torch inclination angle of zero degrees,
the liquid metal at the wire tip flows into the pool due to the
forces of capillary pressure and electro-magnetic forces, as
shown in Figure 1 (a). When high current flows in the liquid
bridge during short-circuiting, the depression in the pool oc-
curs at the breakup of the liquid bridge and, subsequently,
it induces pool oscillation. The time required for breakup of
the liquid bridge dominates short-circuiting frequency and
dictates the welding current necessary for practical welding.
In principle, therefore, only current modulation is available
for use to achieve stable and smoothmetal transfer. When the
wire is inclined to the pool, because electro-magnetic forces
do not act axial-symmetrically, the bridge is deformed like a
bow. And after the breakup of the bridge, the drop at the wire
tip is detached from the solid wire tip and is propelled away
as a spatter, as shown in Figure 1 (b).
For several decades in Japan and Western countries, re-
search and development in the short-circuit welding process
has been focused on realising stable welding that is spatter
free by means of actively controlling welding current alone.
But in practical applications, this has never been completely
satisfactory, because amultitude of welding variation, such as
current, shielding gas and consumablematerial, which restrict
the levels of control possible.
The presentation and publication of the CSC process for
aluminiumMIGwelding by G. Huismann [7] notes that control
of wire feeding speed and direction was very effective for
stabilising the short-circuiting process and reducing spatter.
Simultaneous control of current and wire feeding was then
established, which expanded the available range of applica-
tions possible for the process. By using digitally controlled
welding machines, the breakup of the liquid bridge could be
achievedmechanically, via a precisemovement of thewire tip
under the control of the feeder. Inaddition, currentmodulation
could be used to widen the available range of welding condi-
tions. For example, the combination of short-circuit transfer
with pulsed transfer was developed for the GMAWprocess and
used in practice[8].
To realise a new welding process, however, we need to
start from the concept stage, for which advanced numerical
simulation is an effective tool. Figure 2 shows the numerical
simulation results for metal transfer in an argon gas shielded
(a) Inclination angle = 0°
(b) Inclination angle = 45°.