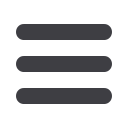

January 2009 Tube Products International
35
f i t t ings
feature on . . .
A custom compact double block and
bleed valve from Parker Instrumentation
is helping to reduce the size and weight
of a groundbreaking skid produced for
the Chevron Tahiti platform in the Gulf
of Mexico.
Built by Test Automation & Controls,
the equipment is believed to be the
largest chemical injection skid ever
produced, and has been designed to
operate at 15,000 PSI, to withstand the
pressures required for operations in the
Tahiti field’s deep, sub-salt reservoirs.
Parker’s integrated valve provides a
15,000 PSI rated double block and
bleed function.
At this operating pressure, such valve
configurations are usually constructed
using discrete components, involving
a large amount of space, extensive
weight, and a large number of potential
leak paths.
The number of components is often
made higher because the cone and
thread interfaces used to make con-
nections at these pressures are usually
fitted with an additional anti-vibration
accessory, to combat the common
issue of vibration-induced problems
associated with threaded connections.
To simplify the project, Parker
Instrumentation suggested an uprated
version of its single-piece 10,000 PSI
double block and bleed manifold, fitted
with the company’s unique 15,000 PSI
rated MPI compression tube fittings.
The resulting manifold is estimated
to have reduced the mounting space
and weight budgets by around 50%,
and replaces around nine individual
components (three valves and six
anti-vibration glands), greatly reducing
potential leak paths.
“The size and
weight reductions contributed by this
manifold have helped to reduce the
topside equipment budget,”
commented
Kevin Burke of Parker Instrumentation.
“The manifold also helps to eliminate
threaded connections, a common
source of reliability problems.”
Parker Instrumentation is part of the
Parker Hannifin group, a diversified
manufacturer of motion and control
technologies and systems, providing
precision-engineered solutions for a
wide variety of commercial, mobile,
industrial and aerospace markets.
Parker Instrumentation Products
Division, Europe
– UK
ipd@parker.com www.parker.comParker Hannifin Middle East
– United Arab Emirates
mamin@parker.com www.parker.comDouble block and bleed valve
Electrofusion fittings
Radius Systems (formerly Uponor) has developed a technologically advanced
electrofusion fitting designed to bring time and cost savings to water service
connection operations. The QuickTEE features an integrated socket that
provides a rapid, single weld, service connection from water main to service
pipe, saving at least three minutes in fitting time per connection. By reducing the
number of joints in the system, the QuickTEE improves overall integrity as well
as reducing the number of parts required on-site (and in the supply chain), by
integrating all fittings needed for the service connection into one part. The base
of the QuickTEE uses Radius Systems’ Unifit range rated technology, making
each fitting capable of working on more than one pipe size.
A built-in clamp mechanism secures the service pipe in place during the fusion
cycle, removing the need for service pipe clamp tools. In trials these integrated
clamps proved popular with installers, ensuring easy compliance with industry
work procedures. QuickTEE service fittings are now being made available in the
UK following a period of trial evaluation by leading water utilities. Installation of
the fittings requires no additional training or any new tooling.
Radius Systems Limited
– UK
sales@radius-systems.co.uk•
www.radius-systems.co.ukSeamless steel
pipe fittings
Unifit Boru Baglanti is a manufacturer
and wholesaler of seamless steel pipe
fittings and flanges.
Using state-of-the-art technology
and experienced staff, the company
manufactures Unifit branded products
with high quality standards. Once
established in the domestic market, the
company extended its activities abroad,
and currently exports to Europe and the
Middle East.
Unifit’s production activities occupy a
6,000m
2
area, with nearby highways
and cargo ports, giving the company a
logistical advantage.
The company is based in Turkey, which
is a member of the European Customs
Union and in negotiations for permanent
membership of the European Union.
Sister company Burak Boru, a seamless
carbon steel stockist, supplies all of
Unifit’s product ranges. Occupying a
leading position in the sector of seam-
less steel pipe trading with its stock
and sales volume, the company
supports many industrial sectors, such
as automotive, HVAC installations,
construction, and naval architecture.
With the basic principle of covering
material demands based on dimensions,
quality, and quantity on time, the
company determines its stock policy
according to customer requests.
The company has a 45,000m
2
stocking
area, with stock capacity of 30,000
tons.
All materials supplied by Burak Boru are
tested in the manufacturing factory and
are certificated according to EN, DIN,
ASTM, API and GOST standards.
The company has a quality management
system, and has been certified to ISO
9001:2000.
Unifit Boru Baglanti
– Turkey
info@unifitfittings.com www.unifitfittings.comBurak Boru
– Turkey
info@burakboru.com www.burakboru.com