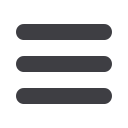

PRODUCT News
46
MODERN MINING
April 2017
Coralynne&Associates+27 (011) 849 3142 • Optimum material flow • Up to 80% decrease in material degradation • Reduced dust and noise levels • Virtually maintenance free • Greatly reduced spillage • Significant reduction in belt damage ABSOLUTE MATERIAL FLOW CONTROL ABSOLUTE MATERIAL FLOW CONTROL SOUTHAFRICA TM Phone: +27 (0) 11 827 9372 Email: info@webachutes.comAutomated tensioner for conveyor belt cleaners
In another move toward ‘smarter’ material
handling, a global conveyor technology
innovator has introduced an automated
pneumatic tensioning system for belt
cleaners.
The new offer ing from Mar tin
Engineering delivers precise monitoring
and tensioning throughout all stages of
blade life, reducing the labour typically
required to maintain optimum blade pres-
sure and extending the service life of both
the belt and the cleaner.
Equipped with sensors to confirm that
the belt is loaded and running, the sys-
tem automatically backs the blade away
during stoppages or when the conveyor
is running empty, minimising unneces-
sary wear to both the belt and cleaner.
The result is consistently correct blade
tension, with reduced power demand on
start-up, all managed without operator
intervention.
“Pneumatic tensioners have some
advantages versus mechanical con-
The system uses the moving conveyor to generate
electricity, powering a compressor to maintain opti-
mum blade pressure.
struction,” explains Product Development
Engineer Andrew Timmerman. “Mechanical
designs work well as long as they are prop-
erly adjusted, but in many cases this requires
periodic attention from maintenance crews
as the cleaning blade wears down. Also, some
operators will loosen a mechanical tensioner
to reduce drag at start-up, which reduces the
cleaner’s performance if not correctly re-ten-
sioned afterward.”
The Automated Blade System (ABS) can be
supplied in two variations, for locations with
or without an existing power source. On sites
with available power, the company will offer a
120/240 V AC version of the system to power
the system’s 24 V compressor. In facilities able
to supply power and also compressed air to
the head pulley, Martin can design the system
so that the panel simply handles the ‘smart’
portion of engaging and disengaging the
cleaner blade.
For locations lacking power access, the self-
contained version uses the moving conveyor
to generate its own electricity, which powers a
small 24 V DC air compressor to maintain opti-
mum blade pressure at all times.
Built around the patented Martin® Roll
Generator™, the new self-powered version
includes a proprietary storage system devel-
oped specifically for this application. With
lead acid batteries to hold the energy, the
system can produce ample power to drive the
compressor, which maintains pressure in the
reservoir to re-tension the cleaner as needed.
The generator can produce as much as 40
watts of power when running at maximum
speed, which is sufficient to run components
such as weigh scales, moisture sensors, sole-
noids and relays, as well as timers, lights and
safety devices. Wireless communication can
be used to transmit directly to a central con-
troller, giving operators a cost-effective way to
access data that has not been readily available
in the past.
Martin Engineering, tel (+27 13) 656-5135