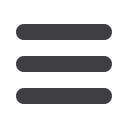

LINKING PEOPLE, JOINING NATIONS
Globalisation in all its aspects has therefore produced many changes to the shipping
industry and also for free-standing maritime structures such as oil rigs. The relatively
small size of many gas fields and the remote location of some make them uneconomic for
development by conventional onshore liquefied natural gas (LNG) processing plant using
subsea pipelines. This has given rise to the development of revolutionary technology by
Shell to construct the world’s biggest Floating LNG (FLNG) production facility which has
the potential to transform the way natural gas resources are developed without the need to
lay pipelines or build processing plants on land.
The FLNG plant, which will produce, liquefy, store and transfer
chilled, compressed LNG directly into ocean-going vessels, will weigh
approximately six times as much as the largest aircraft carrier, some 260
000 tonnes of which will consist of steel, and will measure 488 metres by
74 metres, roughly the size of four soccer fields. When completed the FLNG
vessel will be installed to develop the Prelude and Concerto gas fields in the
Browse Basin, 200 km offshore from the coast of Western Australia. The
FLNG project is global in nature with the hull and topside modules being
built in South Korea; the turret fabricated in Dubai; the subsea structure
in Malaysia; control systems in Singapore and all components coming
together at Geoje, South Korea, one of the world’s largest shipyards.
19
Safety
and quality of welding at all stages of production were lead drivers in the
construction of the floating platform.
Shell’s Prelude floating liquid nitrogen gas facility