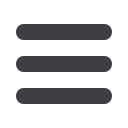
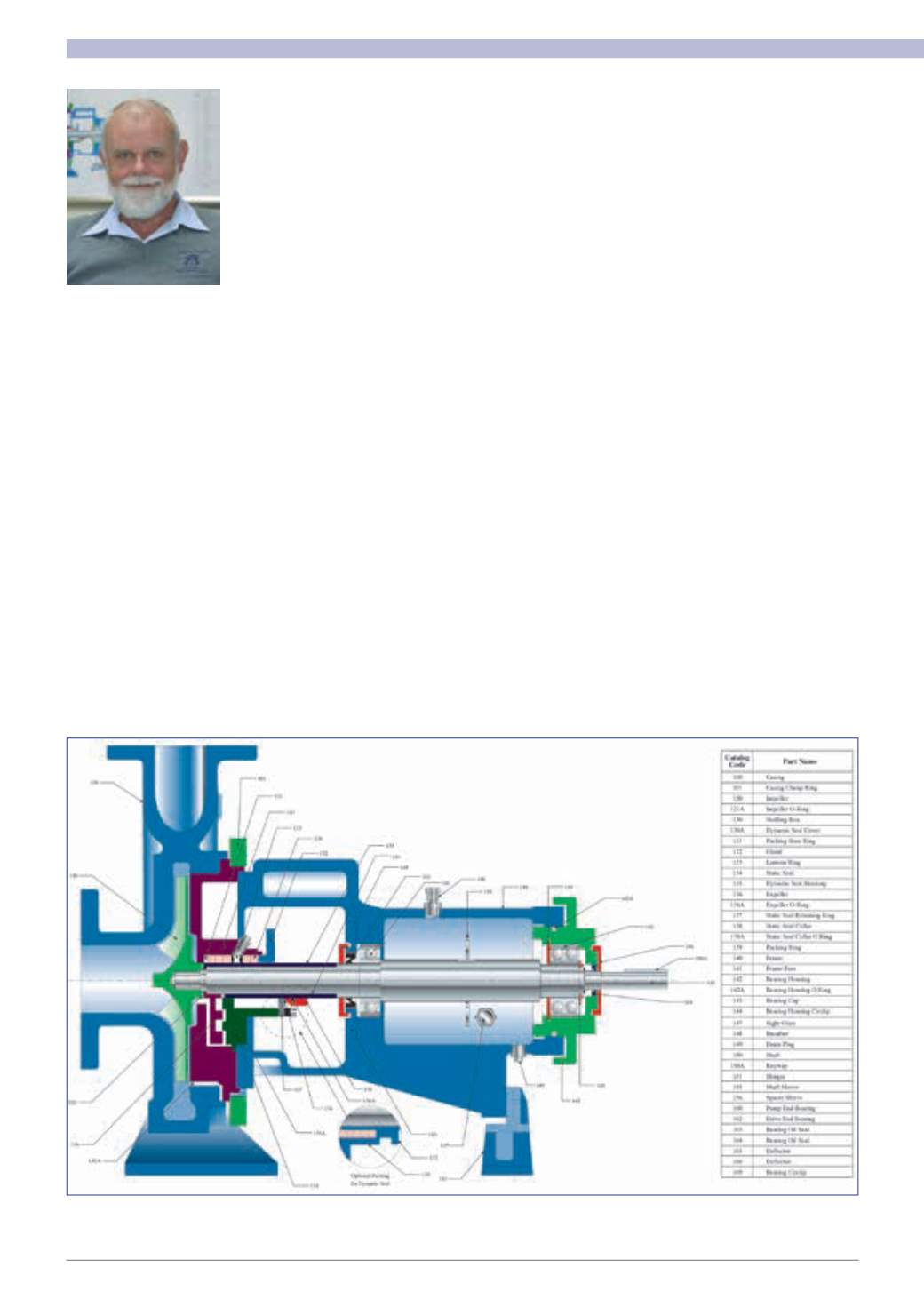
8
¦
MechChem Africa
•
March 2017
S
AM Engineering’s history dates back
tothe1970s,toacompanycalledSan-
dock Austral, which had the license
to locally manufacture Allis Chalm-
ers pumps. “But in the 70s, Sandock Austral
withdrew fromSouthAfrica, leading to a buy-
out by the local manufacturing director, who
bought the casting patterns and secured the
rights to continue tomanufacture the pumps
here in South Africa,” Lubbe begins.
“When ITT purchased Allis Chalmers,
the licensing agreement was extended, but
ITT soon acquired the Gould pumps brand
instead, leaving the Allis Chalmers installed
base across Africa unsupported. So the
SAMCO pump brand was born,” he relates.
Over the years, notable changes were
made to suit the harsh local requirements.
“We addedwear plates to the designs, for ex-
ample, so that thepumps couldbe refurbished
more often and more economically, giving
thema longer life and reducing theownership
costs,” he explains.
SAM Engineering, the manufacturer of SAMCO pumps in SouthAfrica, delivers a variety of chemical
and corrosion-resistant pumps that are custom-made to suit the harsh conditions of the minerals
processing, mining and petrochemical industries as well as the demands of process applications
involving, food, chemicals, pulp and paper and fertiliser.
MechChem Africa
talks to Danny Lubbe,
the company’s sales manager.
SAMCO CP and CPO chemical process pumps are “our stock in trade”. SAM Engineering can manufacture these in 34 different model sizes with 11 different
material combinations.
Specialist
alloys and custom
Mostnotably,though,theSAMEngineering
name is an acronym of ‘Specialist Alloy
Manufacturer’, which reflects a deliberate
strategy to be as flexible as possible when it
comes to alloy choices andmaterial combina-
tion for the SAMCO pump range.
“Ourmotto is ‘customisedpump solutions’
and we live up to that motto by manufactur-
ing our impellers, volutes, wear plates and
bearing frames in the material or alloy that
best suits the actual application,” Lubbenotes,
adding: “We can offer any combination of
11 standard alloys and we have complete
flexibility with respect to novel materials of
manufacture.
“We were the first company to agree to
manufacture skids, bearing frames and the
power-end of our pumps fromstainless steel.
This is abigno-no fromglobalOEMs, whichall
tend to standardise on their frame materials.
Very fewwill agree to custommanufacturing,”
Lubbe suggests.
“Up in places such as the Copper Belt,
the conditions are often terribly harsh and
pumps fail regularly. By supplying stainless
steel frames and customised wet-end alloys,
our pumps are far better protected, so they
last longer and aremore reliable,” he explains.
“Our wet-ends are manufactured in
all kinds of materials: CD-4 wear plates, a
wear- and corrosion-resistant duplex alloy;
impellers and volutes frommaterials such as
316, duplex and super duplex stainless steels;
or Alloy 20, a nickel-chromium-molybdenum
alloy that is ideal for sulphuric acid applica-
tions. We strive to offer the highest corro-
sion resistance possible for the media being
pumped,” Lubbe advises.
Long serving SAM Engineering clients
include customers such as Tongaat on the
food side and SAPPI, for pulp and paper. “For
pumping pulp and liquids with solid content,
weuseopen impellers. Thesehaveno shrouds
on the inlet side so that solids can be easily
dischargedwithout clogging thepump,” Lubbe
tells
MechChem Africa
.